Maximize productivity with the right robot system
Experience counts.
The right robot in the right place on a production line reduces non-productive time, increases productivity, and ensures reproducible results.
SW has a clear opinion on automation and can back it up with countless practical examples. Every robot must be matched to the workpiece, the respective machine, and the machining processes. Above all, robotic systems must reduce complexity. In this way, they enable productive interlinking of machines and systems with minimal engineering and commissioning effort. SW Automation knows these challenges and has already equipped numerous production lines with automation systems.
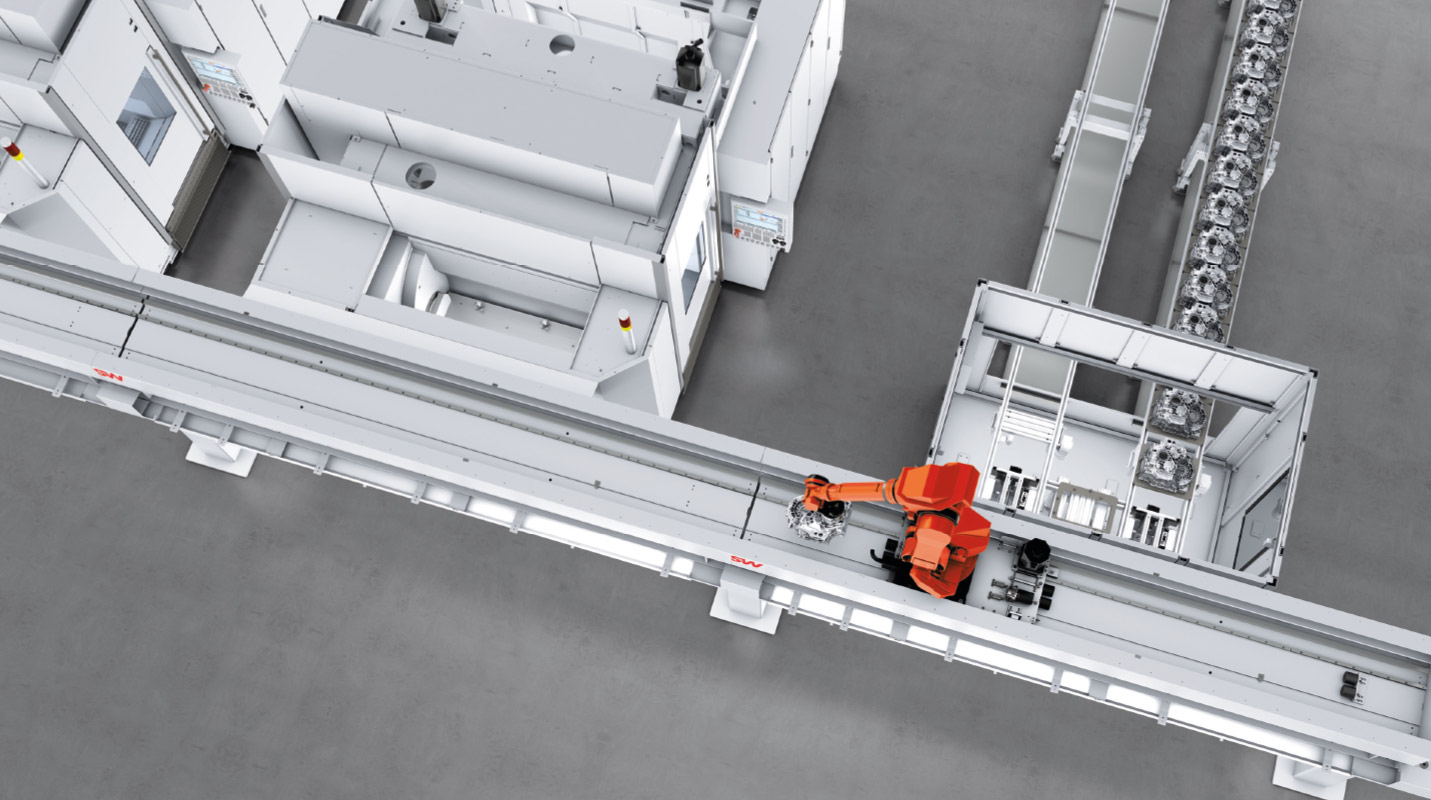
Loading from above eliminates protective fences
Typically, robotic systems from SW load and unload the machine from above. This saves space and expensive protective enclosures because the industrial robots are designed to not pose a risk to humans. This allows operators to keep an eye on the workspace of the CNC machining centers at all times, and maintenance personnel have free access to all important components of the machines. The linking of the machine tools for the complete machining from the raw part to the finished component takes place via a gantry axis above the machining centers. On this modularly expandable axis, independently moving 7-axis robots take over the automation of all loading and unloading processes, including necessary fixture changes.
Fast commissioning and maximum throughput
Robotic systems have a reputation for being very complicated to commission. The Technology People disagree. They plan each robot system with state-of-the-art simulation programs and virtually optimize the motion sequences before commissioning. This minimizes unproductive downtime in advance and ensures maximum output in production.
Seamless communication with the CNC controls of the machining centers and the higher-level MES/ERP systems is crucial. SW Automation has already programmed these interfaces and adapts them on a project-by-project basis. CNC controls and robot controls are therefore perfectly matched to each other. The cross-vendor protocols OPC UA or MQTT for data exchange between Operating Technology (OT) and Information Technology (IT), which are established in the market, are already pre-installed. In addition, SW Automation uses a modular construction kit of highly available standard components and standard robots.
Flexible for new tasks
The trend towards shorter product life cycles also poses new challenges for manufacturing. Processes have to be changed or new components manufactured much more frequently than before. Intelligent robotic systems support such flexibility. The standard 7-axis robots in different performance classes adapt the motion sequences to the respective workpieces. Within the production lines, users can swap the positions of the machines and machining centers or remove individual machines and set them up in a different location without having to mechanically intervene in the robot system. You can easily integrate peripheral stations for brushing, deburring, washing, or preserving, even at a later date. This protects SW’s investment in robotic equipment over the long term and increases return on investment (ROI).
Transparent and reproducible processes
Robotic systems minimize personnel costs and maximize productivity at the same time. They also create complete transparency because with robotic systems, all movements are traceable and reproducible, error-free. What’s more, the storage of all production data, including material handling, enables complete traceability, an increasingly common requirement of OEMs They also support the digital transformation of manufacturing and fit seamlessly into the concepts of the Industrial Internet of Things (IIoT) and Industry 4.0.
Consider the advantages of customized automation solutions for your production and contact our Technology People if you have any questions.
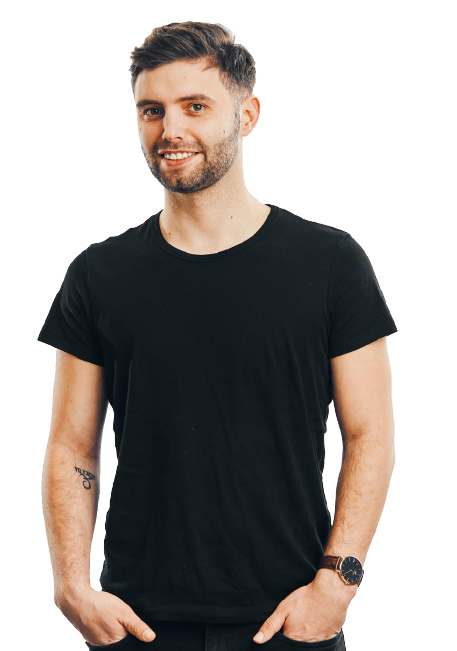