Independent manufacturing cell
– the factory within the factory
SW develops the perfect automation solution for you. Our specialists consider the workpieces, the machine tool, and the processes for optimal automation of your production and turn a CNC machining center into a self-sufficient and flexible manufacturing cell. As a system, it highly efficiently encapsulates the complete machining of workpieces and, in conjunction with multi-spindle machining centers, enables rapid scaling of quantities. By using multiple autonomous and flexible cells, production lines can cover multi-variant manufacturing or efficiently produce families of parts with different sizes.
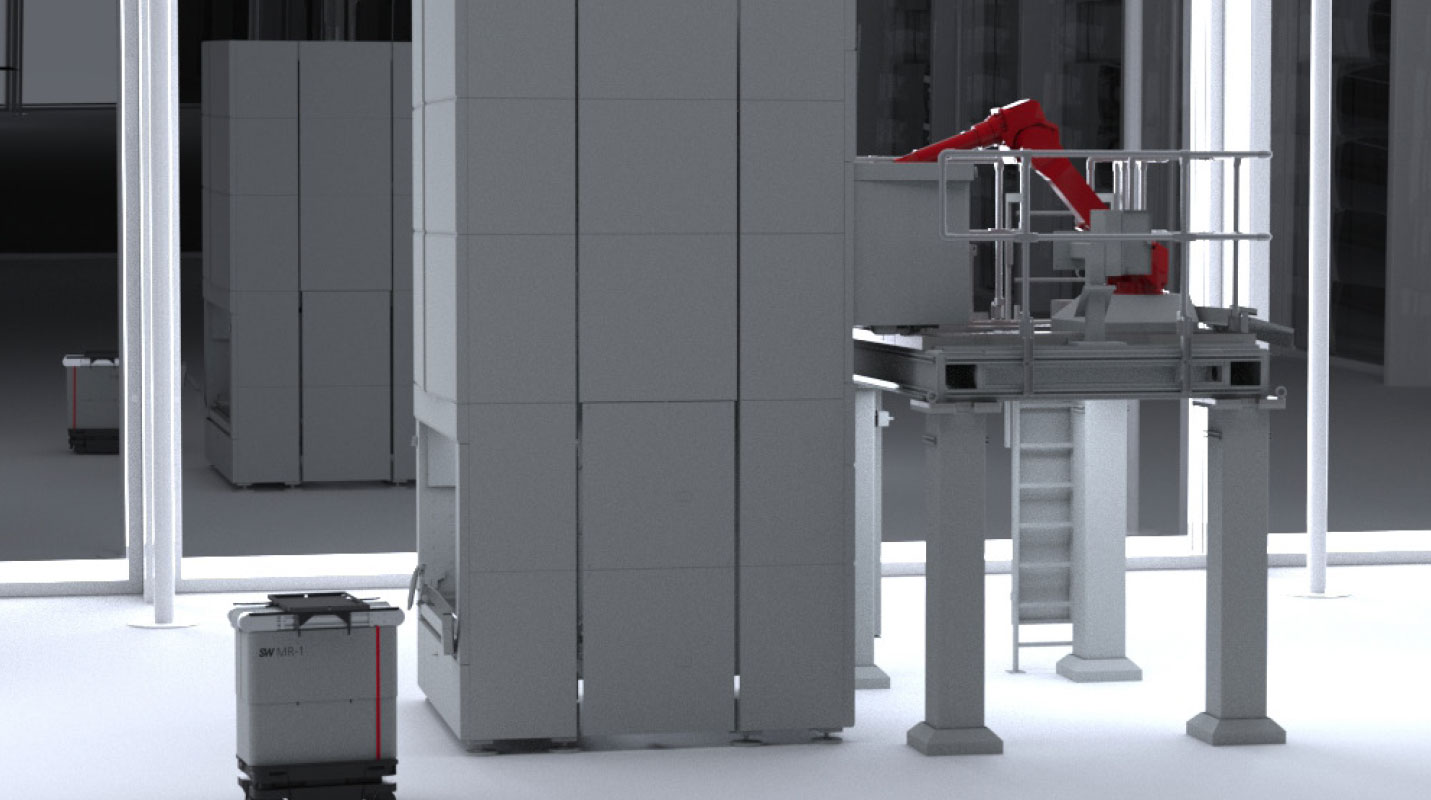
Automatic
placement by AGV
Depending on the size of the workpieces, self-sufficient and flexible production cells are equipped with a loading module or a pallet store that is filled with blanks at the beginning of the shift. This can be done manually or automatically, with SW’s Automated Guided Vehicle (AGV) the MobileRob. The MobileRob independently creates a map of the environment and navigates the factory floor without markers. Equipped with a variable-height table, it automatically loads the loading module or pallet storage with workpieces and fixtures.
TECHNICAL DATA | DETAILS
About the operation of the self-sufficient manufacturing cell:
|Unloading requirement: Pallets with finished parts are provided in sequence for unloading
|Loading requirement: Free spaces for receiving pallets of unfinished parts are provided
|No possibility of manipulation by the operator
SW offers these options for automation:
|Pallets with identification
|Blank selection according to NC program
|Camera surveillance
|Workpiece cleaning
|Connection of the AGV MobileRob for automatic loading and unloading of the storage tower
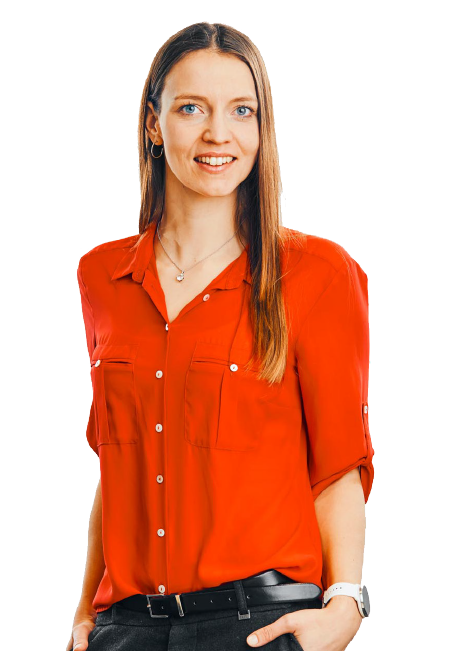