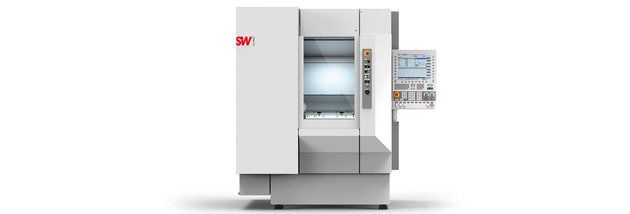
Two-spindle BA W02-22 with wear-free direct drive technology shortens cycle times in precision mechanics
Schramberg, 18.04.2016. Equipped with linear and torque motors in all feed axes, the new BA W02-22 two-spindle machining center from Schwäbische Werkzeugmaschinen GmbH (SW) sets new records for short cycle times and maximum precision in 5-axis machining. The extremely compact machine with a spindle distance of 250 mm produces complex workpieces from non-magnetic materials highly efficiently on a footprint of just under four square meters.
“Wear-free direct drive technology ensures the lowest total cost of ownership thanks to significantly shorter cycle times and higher availability,” emphasizes Reiner Fries, Managing Director Sales at SW. With the new BA W02-22, the leading supplier of multi-spindle machining centers for medium and large series is primarily targeting precision engineering applications, for example in the watchmaking industry or the automotive sector. There it is also suitable for high-precision free-form surface machining of impellers.
Chip-to-chip in 1.75 seconds
The linear feed axes accelerate at up to 24 m/s² to a rapid traverse of up to 120 m/min. The liquid-cooled HSK A40 motor spindles in AC synchronous technology run up to the maximum speed of 25,000 rpm within 0.7 seconds. The chip-to-chip time for a tool change is only 1.75 seconds. Loading and unloading takes place in parallel with the main time via the double-swivel beam. There, SW has integrated two independent rotary tables driven by torque motors with a direct angle measurement. If required, these can be equipped with integrated hydraulic workpiece clamping systems.
Doubled Kv factor shortens cycle times
Compared to ball screws, the BA W02-22 with direct drive technology achieves twice the Kv factor and a wear-free jerk of 1,200 m/s³ for high-precision micro movements. “Thanks to the extremely low weight of the rotary axes, the high dynamics and the short non-productive times, our smallest family member reduces the cycle time by a double-digit percentage compared to conventional machines,” Reiner Fries emphasizes.
Even at the highest machining speeds, the compact machine achieves a positioning accuracy of less than 0.006 mm. The electronically coupled gantry drive for the Y-axis contributes to this even with off-center loads. The virtually complete hydraulic weight compensation of the vertical axis increases energy efficiency and thermally relieves the Y-feed motors. The 3-axis unit is designed as a “box-in-open-box” with very small and low-mass machining units. The SW-specific design allows free access from the rear of the machine for service and maintenance work. The chip- and splash-proof tool magazine, which can be loaded directly from the workstation, offers 40, 80 or 120 places in modular form.
With the new, currently smallest, two-spindle machining center with linear motors, SW covers finely scaled spindle distances of 250, 400, 600 and 800 mm.
You will also receive the appropriate image material for our press releases. Please contact us if you are interested.