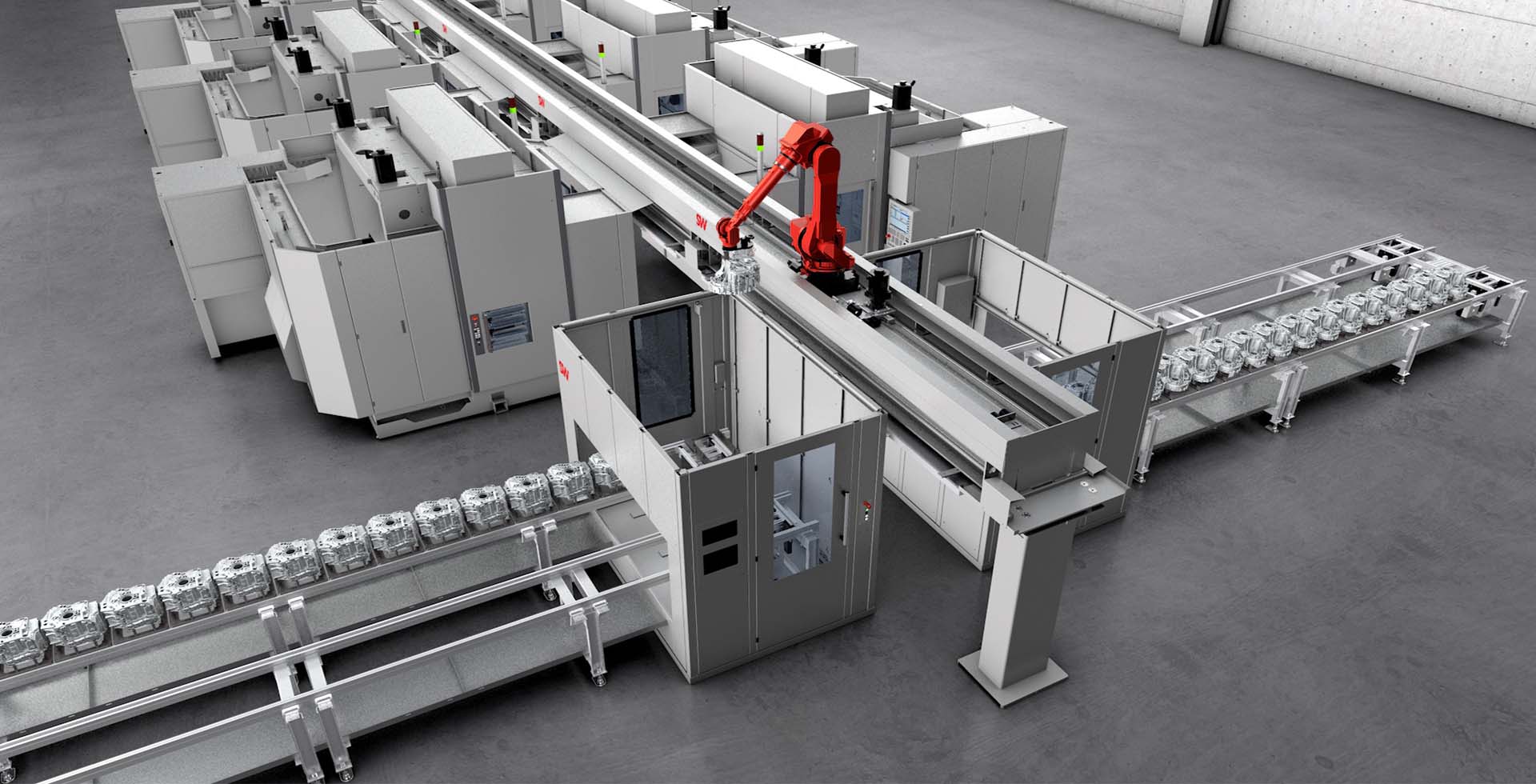
Schwäbische Werkzeugmaschinen GmbH (SW) is presenting its broad portfolio for automation at automatica in Munich. With highly efficient machining centres, integrated automation solutions, autonomous manufacturing cells, highly automated production lines, innovative software solutions, digital and physical services, the company increases the productivity of its customers.
Flexible automation solutions – modularly expandable, freely accessible and safe due to second level
With the automation modules from SW, CNC machining centres and peripheral stations can be optimally linked to form highly productive production lines or operated in a matrix production.
The TopRob7 automation module is a gantry axis at a height of 2 m that loads and unloads machines and systems process-oriented from above. Thanks to this design, there is no need for protective fences, there are no more trip hazards such as oil pans on the floor and valuable space can be saved in the workshop. By using the second level, the operator also has an unobstructed view into the work areas and the components of the machine tools are directly accessible during maintenance.
Due to the additional seventh traversing axis, more processes can be interlinked with the TopRob7 than with 6-axis standard robots. Workpieces of different weights and sizes can be changed as well as entire fixtures of the linked processes. Even complex components and component families can be precisely positioned, which increases the productivity of the system. The automation modules comply with Industry 4.0 standards and are thus eligible for funding in this area: they communicate directly with the machine control and higher-level systems.
In addition, the TopRob7 allows modular extensions: If the number of pieces increases, additional, independently operating machining centres and robots can also be integrated into it at a later date. When the number of pieces decreases, CNC machining centres can be taken out of the line and used for other production tasks.
The automation module TopRob6, for example, which is designed for one to two processes, is also suitable for the automation of individual machines. Together with a storage tower, it forms the central building block of efficient loading units and – in line with SW Automation‘s modular concept – can be linked to SW‘s other automation modules via standard interfaces.
The MobileRob, an Automated Guided Vehicle (AGV), can be used for the internal transport of workpieces. For example, it supplies machine tools and systems with raw parts and removes processed parts without a driver. It creates a position map without programming and orientates itself independently. The system can serve as an essential component of matrix production by linking production lines to form adaptive process chains in which individual components only run through the order-specific processes required.
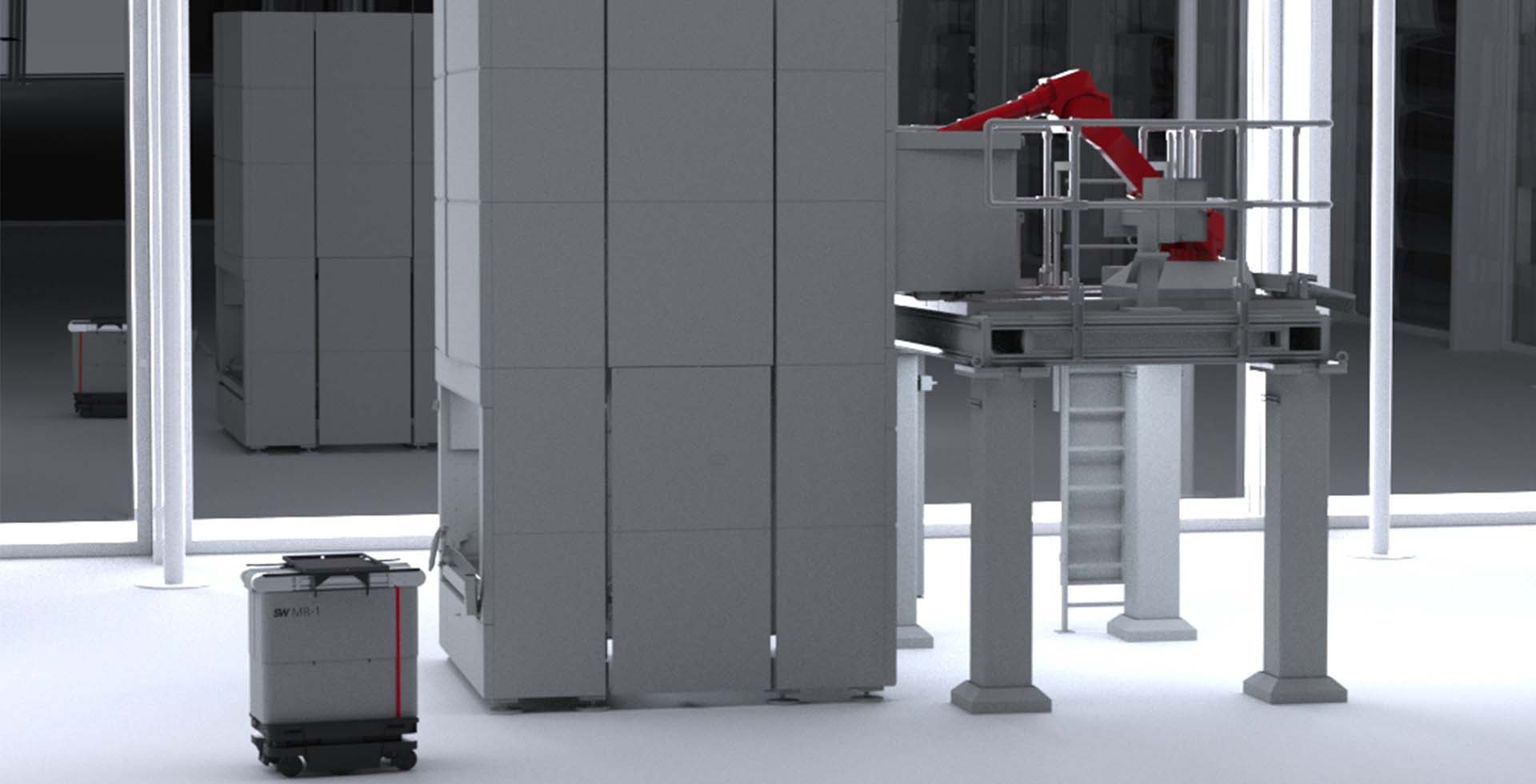
Reproducible quality and more efficiency through individual automation solutions in assembly
Pressing, joining, screwing, gluing, coating – SW Automation designs individual solutions for assembly automation that increase efficiency in automotive manufacturing. Employees are deployed precisely where their flexibility and intuition are indispensable.
Together with the customer, SW Automation designs a modular overall concept from individual components that effectively combines individual assembly processes. The focus is on essential requirements regarding the traceability of all assembly steps, productivity and reproducible quality with zero error rate. SW Automation combines fully automatic stations with semi-automatic and ergonomically designed manual workstations to form complete assembly lines. The company also implements assembly lines for component families as well as variant-rich assembly and links them to the customer‘s higher-level MES and ERP systems. For example, SW Automation has created a concept for the automatic assembly of half shafts with comprehensive process data acquisition and backup.
In addition, SW Automation integrates and automates all peripheral stations that are necessary to completely manufacture components. The company has decades of experience in integrating secondary processes into highly automated lines; from cleaning, deburring and measuring to leak testing, welding and tempering, right through to packaging.
With a proven network of suppliers for special technologies as well as experts for automation, the company puts together the optimal production line as a complete solution – ready to connect and from a single source.
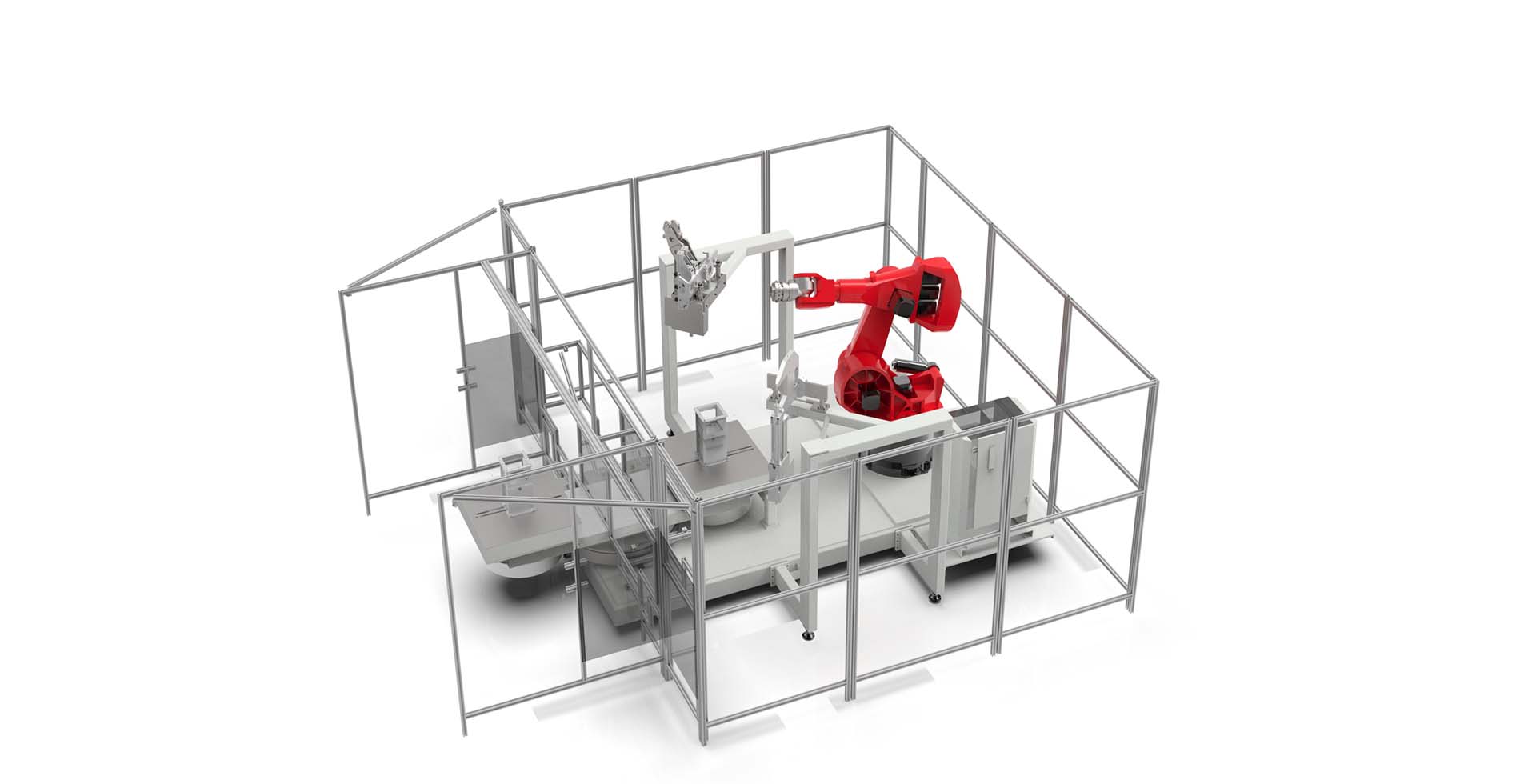
Modular automation in the automotive industry
Until now, it was common in the automotive industry to purchase an individual system for the automated production of a specific product or workpiece. This investment paid for itself due to the plant and product runtimes of almost ten years each. But the situation is increasingly changing: production capacity utilisation with a single product type produced in high volumes over a long period of time is only possible in rare cases. In addition to the decreasing product quantities and runtimes, there is also an increasing variety of series products that can no longer cope with the long plant runtimes.
SW Automation, a subsidiary of Schwäbische Werkzeugmaschinen GmbH (SW), recognised at an early stage that this discrepancy can only be eliminated through very flexible, modular automation solutions. The company‘s development from a special plant manufacturer to a supplier of modular automation solutions reflects this realisation and shows how the company is meeting future market requirements.
SW Automation GmbH was founded in 1998 as a special plant manufacturer near Friedrichshafen on Lake Constance. The company designed solutions according to special requirements for large-scale industry based in the region, ranging from workpieces of various sizes to assembly automation. In order to make the development and construction of the unique systems more efficient in the future and to take into account the changing requirements in the automotive sector, the company began designing an automation platform based on a modular system in 2014. Its standardised modules can be combined into an individual system according to the respective production concept and application. “We see ourselves as an architect of manufacturing plants, especially for Tier 1 and Tier 2 suppliers in the automotive industry. Currently, seven standard modules are already available in the company‘s modular system”, explains Makis.
Standard interfaces allow adaptation in the field
The entire engineering process, from mechanical to software design, is carried out in-house. The assembly of the manufactured parts is also carried out by SW Automation, as are final installation, commissioning and service. The standard modules are plug-and-play compatible with SW machine tools as well as systems from other manufacturers. “Since the variable and flexible interlinking takes place via standard interfaces, downstream processes or third-party machines can also be integrated into the overall system, and subsequent adjustments in the field, including system downsizing, are easily possible,” explains Makis. In order to achieve increased availability, the automatic connection of the processes is not firmly coupled, but automatic buffers are installed, for example, so that failures can be better cushioned. The basic modules – for example for machine assembly or subassembly – are designed by SW Automation so that they can be used for as many product variants as possible. They can be supplemented as needed with individual, more customised components. A modular robot, for example, does not only have a single hand to lift cardan shafts or housings with different outer contours from the conveyor and place them in the machine.
To enable even more flexibility for the entire production plant, the individual plant controls are also connected to the SW platform. SW products and the machines provided by the customer for downstream processes are brought together in this higher-level control system. The software allows central access to the plant status, control of production orders, item-related data storage and retrieval for traceability purposes, remote maintenance functions, KPIs and web visualisations.
Turnkey solutions for automated production
SW Automation thus offers complete turnkey solutions in association with SW, which include all components up to the control of the complete system. In addition, the company also designs automation solutions outside of machining and independently of the parent company‘s machine tools. For example, the company develops systems for assembly automation, such as for the processes of screwing, joining and gluing. These systems also benefit from a connection to the SW platform.
Thanks to the modular principle and the other services provided by SW Automation, the entire automation concept no longer needs to be changed for individual product changes. In view of the increasing number of variants and shorter product runtimes, this ensures long-term investment security for automotive suppliers.
“For an optimal solution, we plan the entire process chain with the customer, from the individual component to the packaged product, and configure a modular-based flexible plant concept”, said Sven Makis, Managing Director, SW Automation.
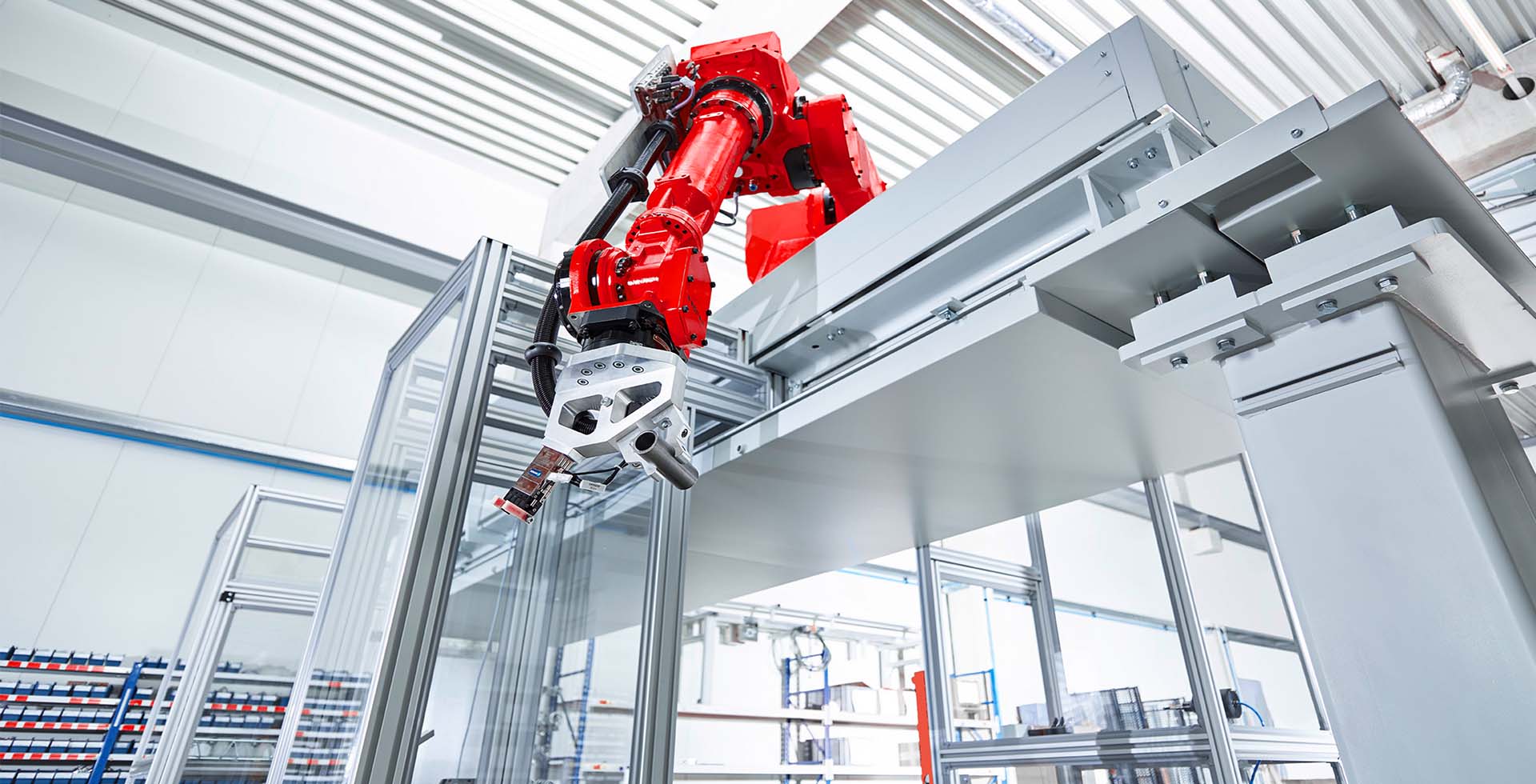
More productivity and availability in manufacturing through digital services
SW has product-, consulting- and research-related digital services in its programme. The core element for most digital services is an IoT gateway for the fast and uncomplicated connection of existing manufacturing systems to the Internet of Things (IoT). It offers scaling options as well as standardised interfaces and ensures that the information only reaches where it is needed via configurable data acquisition and transmission.
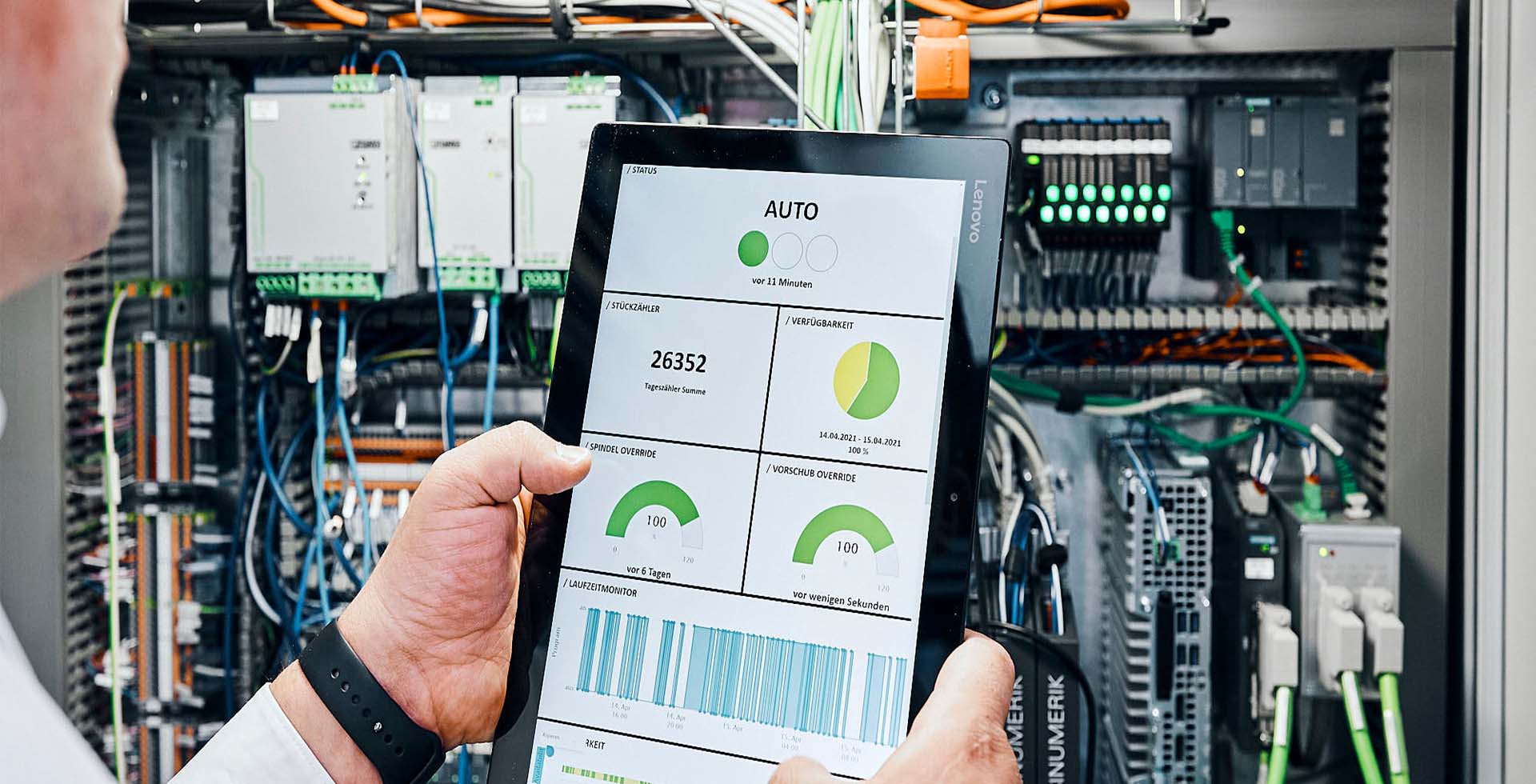
The product-related services include the SW CloudPlatform (SWCP). With its help, the functionality of connected machines and automation solutions can be monitored online. This makes it possible to detect downtimes in good time, reduce operating costs and increase plant efficiency. The SW ScadaPlatform (SWSP) increases transparency through valid key figures and complete workpiece traceability. Causes of quality deficiencies within the workpiece production can thus be detected immediately and countermeasures can be initiated. In addition, SWMP API ensures that machine and automation data flow efficiently to local MES or ERP systems. The interface allows data from SW machining centres to be collected and visualised directly in these systems at the customer‘s site. All customers who opt for integration determine themselves which of their data is included and to what extent.
Consulting-related services include material flow simulations in the digital twin of the plant (Plant Simulation): Already in the project planning phase, SW can virtually set up the customer‘s automated line in state-of-the-art simulation environments and optimise the subsequent production flow. Digitalisation consulting for process optimisation is also possible. The company supports the definition of digital services and their roll-out in production. SW also offers the life data services to other machine and plant manufacturers as an EcoSystem, so that they can quickly start digitisation. SW develops further services via data analytics: Through exchanges with scientists, the company designs new algorithms that can process data and detect anomalies in it.
In addition, there are further life services with which SW accompanies all plants and automation solutions throughout their entire life cycle. In addition to life data, these include life startup for the smooth start-up of production, the training offers of life academy, the reactive service life help, the spare parts sales and repair service life parts, and the life upgrade module with services that bring machining centres and automation solutions up to the current state of the art.