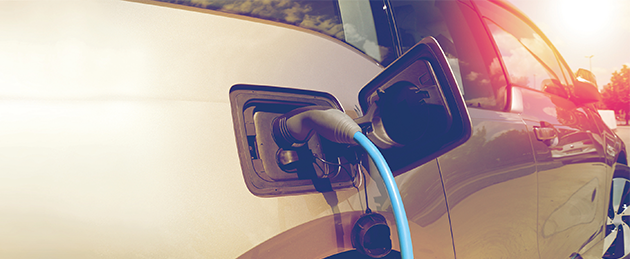
2021 marks the breakthrough for electric vehicles
TIER1 and Tier2 suppliers are therefore currently working on qualifying the production of new lightweight components and preparing for rapid scaling of volumes. Already in use on numerous projects: multi-spindle SW machining centers and those with extra-large working space.
The figures speak for themselves: in terms of new registrations in Germany in 2021, passenger cars with alternative drive systems will have captured a market share of 43 percent. According to the Association of International Motor Vehicle Manufacturers (VDIK), more than 680,000 electric vehicles were newly registered in Germany last year, an increase of 73 percent. Consumers can already choose from more than 140 different car and commercial vehicle models.
For automotive suppliers, the task now is to validate the series production of new components in line with the OEMs’ high quality requirements and ramp them up very quickly. On the one hand, they have to economically scale smaller and medium-sized components with demanding geometry – such as scroll compressors or stator housings – with high precision. On the other side of the spectrum are large structural components such as battery housings, which require very large workspaces for machining. In recent years, SW has developed appropriate manufacturing solutions that are already being used in series production by renowned suppliers.
Lightweight construction is the trump card
In electric vehicles, weight plays a decisive role in range, one of the most important selling points. That is why only light metals are used. SW offers several BAZ series designed for machining non-ferrous metals. All feed axes are equipped with highly dynamic linear motors. They reduce non-productive time and combine the highest cutting performance with extreme precision.
Scale quickly
The massive gain in market share by electric cars is leading OEMs to adjust their medium-term production plans. The result: demand for corresponding components is growing much faster. Here, suppliers achieve particularly fast ramp-up curves with multi-spindle machining centers from SW. SW machining centers manufacture a corresponding number of components in parallel in 2-, 3-, and 4-spindle variants. This saves up to 60 percent floor space and up to 50 percent energy compared to the corresponding number of single-spindle machines and achieves up to 30 percent shorter chip-to-chip times.
Scroll compressor
Scroll compressors play an important role in electromobility for cooling the battery during charging and for the e-motor. SW’s Technology People have applied their extensive process experience to these new components. Complete machining takes place in just two setups in the BA W02-22 two-spindle machining center. As a self-sufficient manufacturing cell with integrated automation, it economically covers medium series. The integrated workpiece magazine enables self-sufficient automatic operation for six to eight hours without manual intervention, depending on the component size. For large-scale production, SW has already implemented complete manufacturing systems with all turning and milling operations as well as end-to-end automation.
Larger components such as stator housings for electric motors are machined highly efficiently by the BA W06-22, which also has two spindles. It is also equipped with linear motors and is one of the fastest CNC machining centers in the world. Stator housings require complex 4- and 5-axis machining with numerous drilling and milling operations.
XXL: Battery case
For the production of large structural components such as battery housings, there are very few machines on the market with sufficient working space and, at the same time, high precision. The BA space3 from SW accommodates such large workpieces with a working area of 3,000 x 1,800 x 875 mm. It is used, for example, in the series production of a battery housing for a battery electric vehicle (BEV). The housing with the dimension of 2.4 x 1.6 meters weighs 115 kg. A particular challenge is the torsion-free clamping concept for 4-axis machining. SW also customizes complete manufacturing systems with fixture construction, tooling concept and automation.
You will also receive the appropriate image material for our press releases. Please contact us if you are interested.