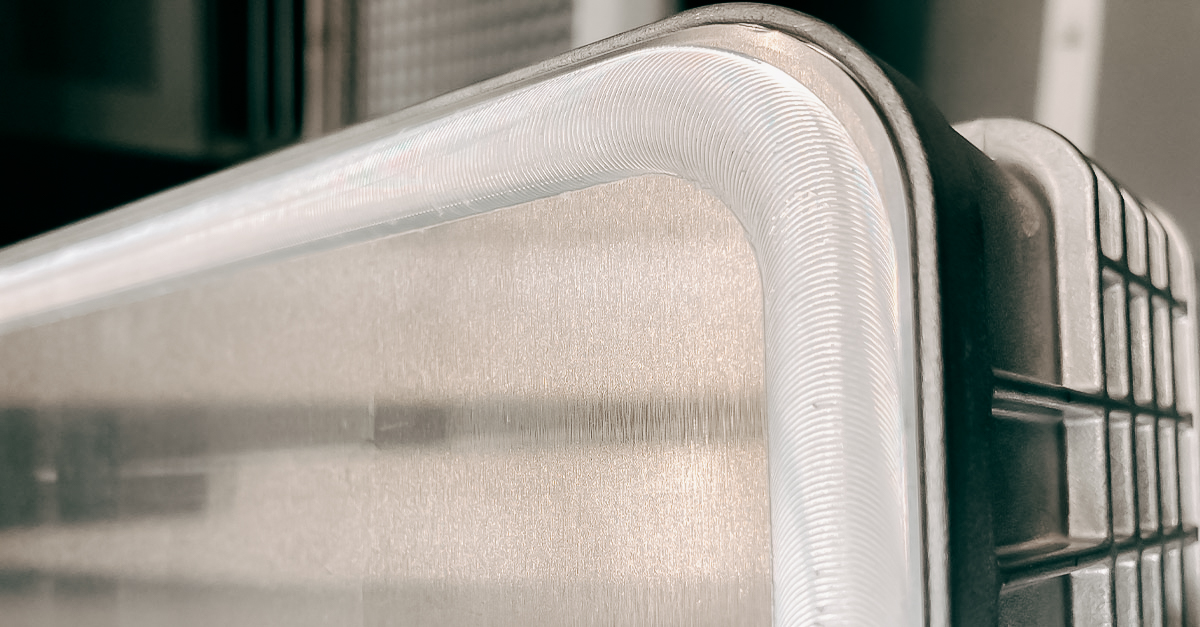
Friction Stir Welding (FSW), is a welding process that creates a strong bond between two metal parts without producing molten metal. Instead, the metal is heated and plastically deformed by a rotary motion and a linear motion to create a strong joint. The process was developed in the 1990s by The Welding Institute (TWI) in the United Kingdom and is now used in a variety of industries, including aerospace, automotive and shipbuilding.
Friction stir welding involves pressing a rotating tool onto the contact surface between the parts to be joined. The friction of the tool with the metal generates heat that softens the metal without melting it. The tool is moved along the contact surface, forming the metal and creating a strong joint.
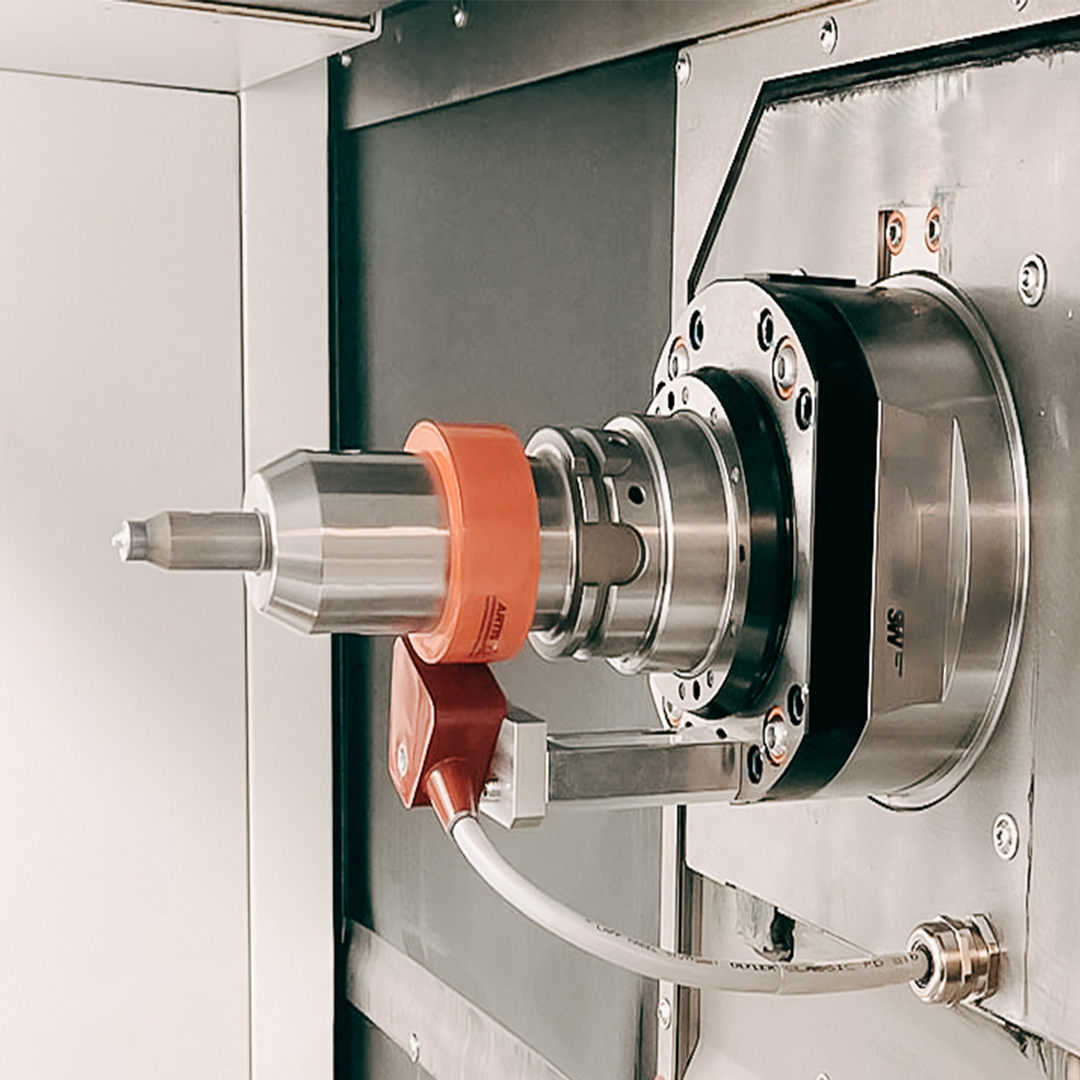
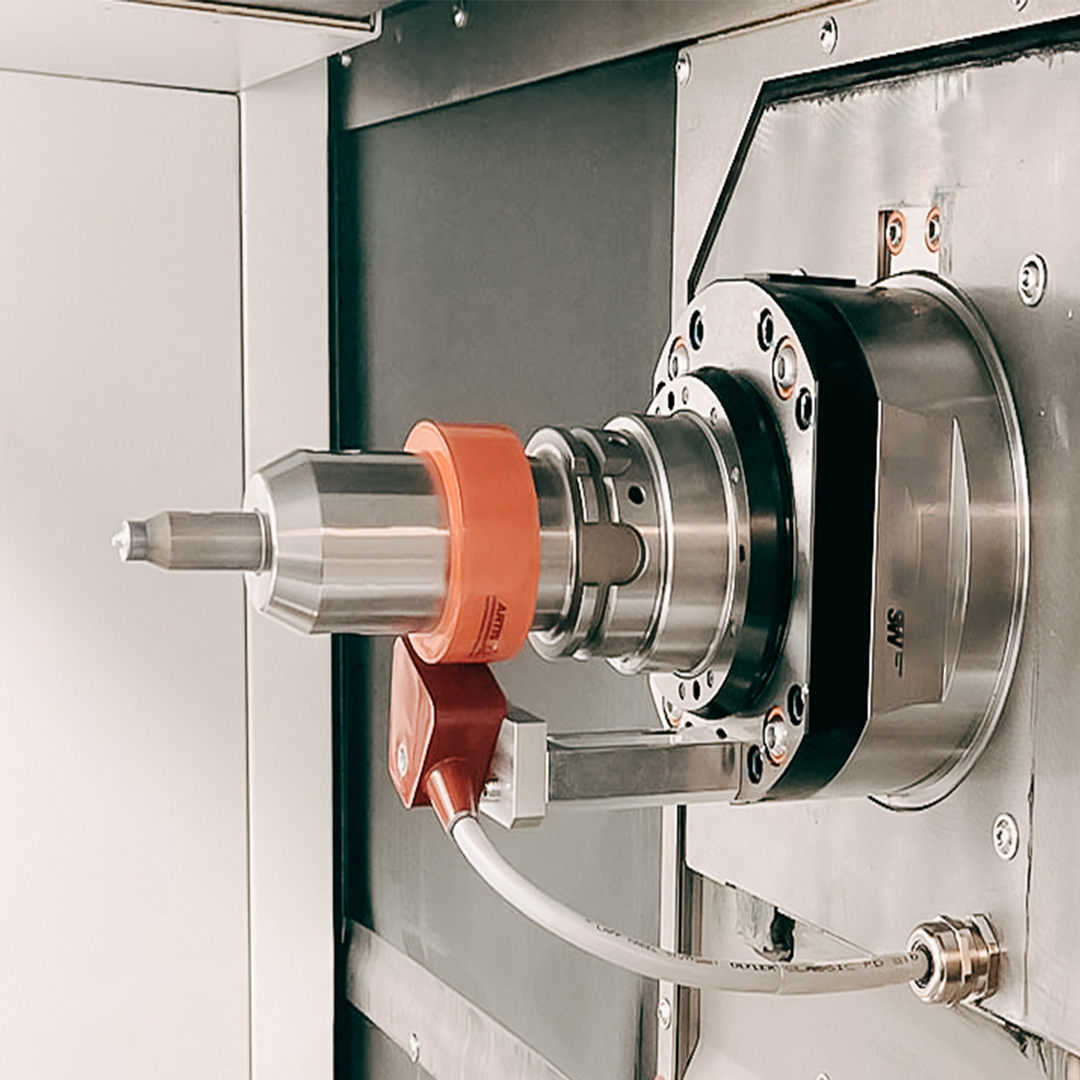
Benefits
- Very high welding speed
- Pressure tight welds
- Low deformation
- High joint strength
- Resistant to cracking and fatigue
- Low deformation and distortion, as no melting occurs
- No emission of pollutants in contrast to arc or laser welding
- Wide range of applications: aluminum, copper, magnesium
- Lower costs due to high welding speed and low post-processing
The process is increasingly being used in e-mobility for high-quality welded joints such as large battery housings and electronics housings. The welding of cast housing and cover ensures a pore-free and medium-tight joint with minimum heat input.
The integration of friction stir welding is basically possible at SW in all machine series. The speeds & feeds for friction stir welding must be adapted to the axis forces of the machine. Independent Z-axes are recommended for multi-spindle welding. By using single and multi-spindle machining centers, upstream or downstream machining operations can be combined, thus significantly increasing efficiency compared to conventional friction stir welding systems.
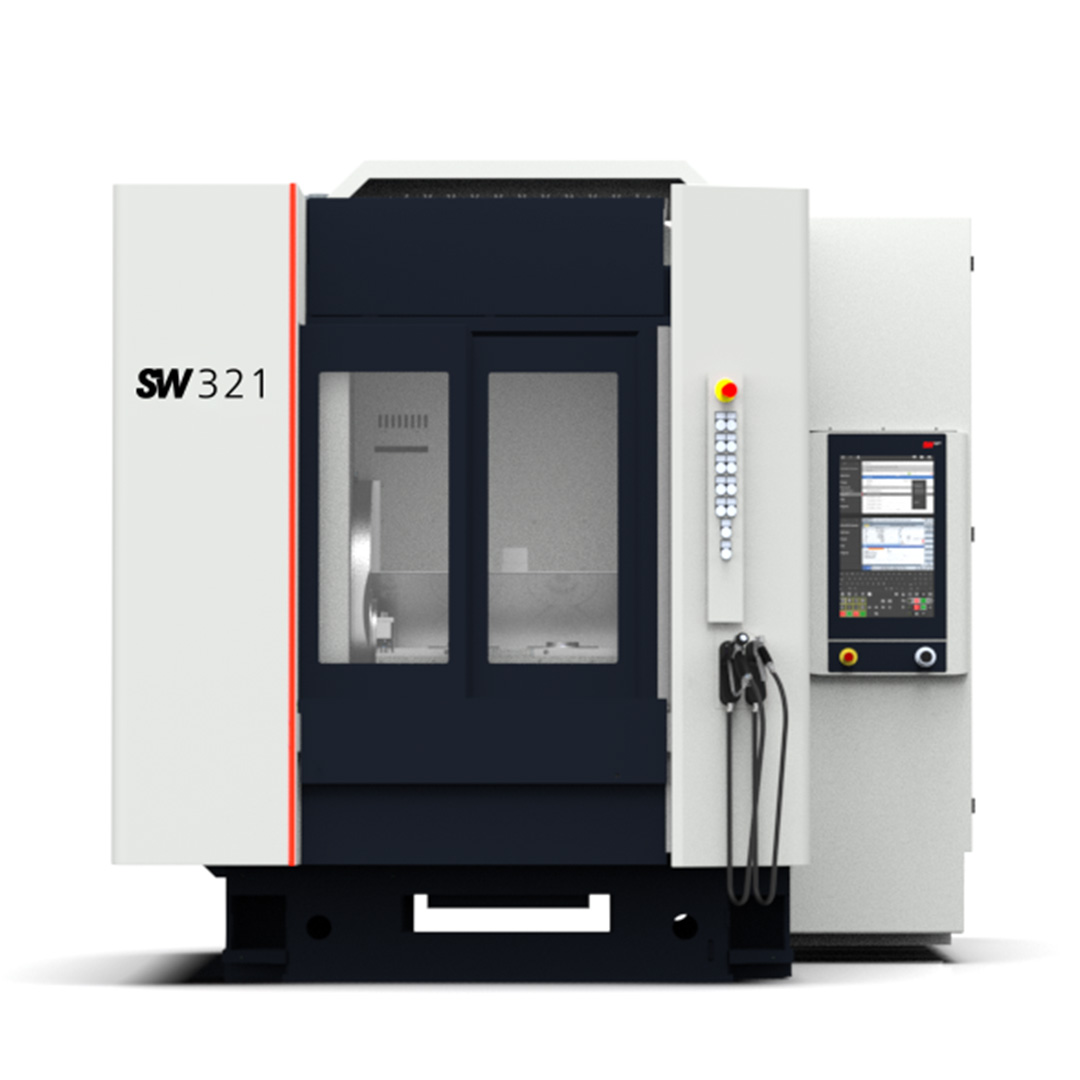
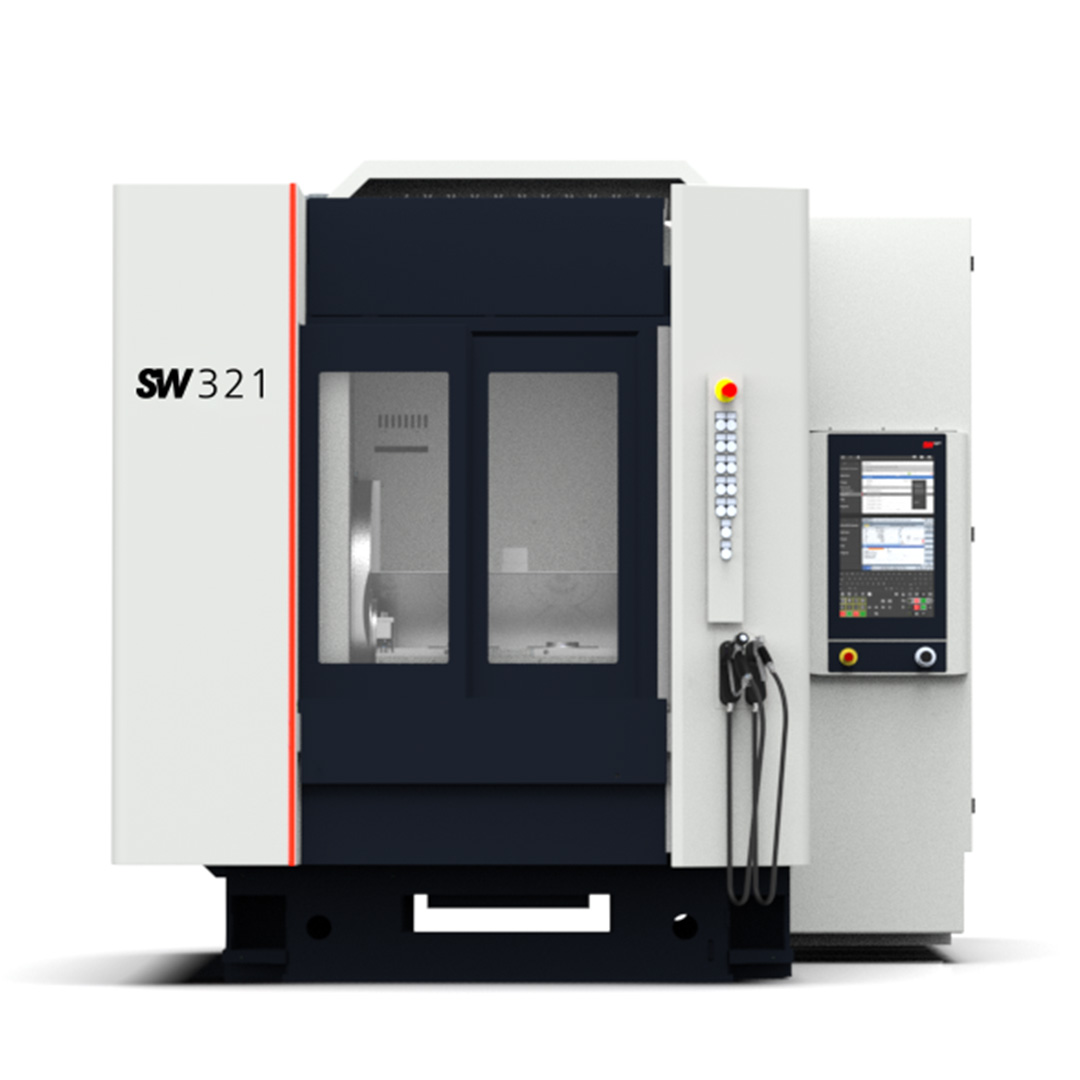
Connection.
Your contact
for friction stir welding:
Patrick Schneider
+ 49 7402 747480
patrick.schneider@sw-machines.com