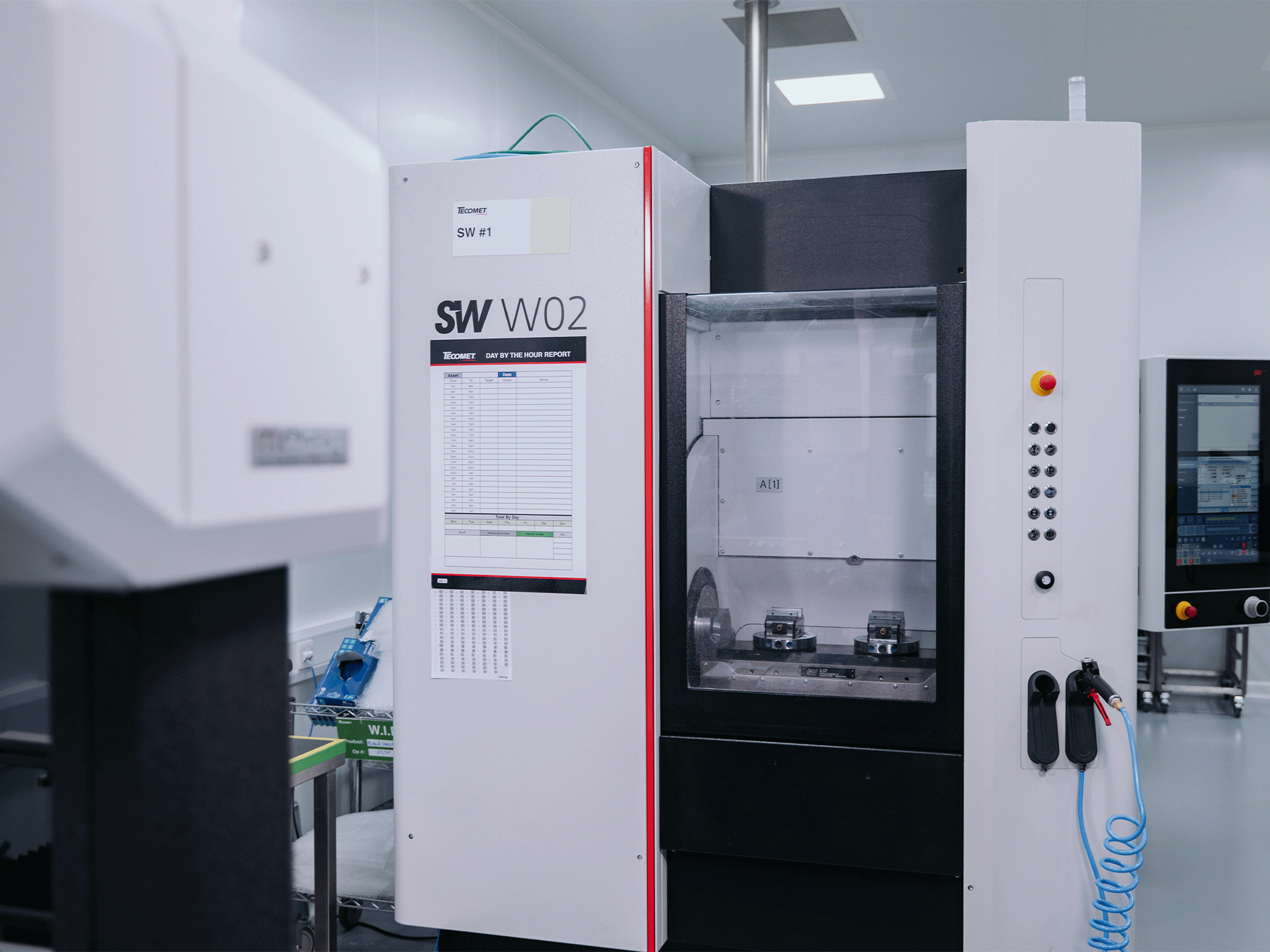
Multiple part sizes and multiple configurations, high quality requirements with tight tolerances, complex production processes, and high volumes that must be manufactured as quickly and efficiently as possible: poly manufacturing for the orthopedics industry faces several challenges. The Irish expert Tecomet relies on two-spindle machining from Schwäbische Werkzeugmaschinen GmbH (SW), which helps to increase their knee implant production per operator and achieve an overall equipment efficiency increase.
Tecomet is a leading metal and materials innovator and contract manufacturer for medical device markets. The site in Cork, Ireland, serves as the Center of Excellence for Medical Device Poly Manufacturing. Here at Cork, over 100 employees work on solutions for the orthopedics industry, producing large volumes of metal and polyethylene parts for medical implants. For knee implants alone, several hundred tibial inserts are manufactured weekly and around the clock. In this tightly scheduled manufacturing process, low downtimes and overall equipment efficiency are crucial to meet customers demand and quality requirements. “Up until 2022, we only ever used single-spindle machining centers in our tibial poly insert production line,” Peter Grehan, Engineering Manager at Tecomet, says. “While these machines work well, we knew there were faster and more efficient machines out there. The single spindle / single table machines require frequent manual interventions switching between Op1 and Op2 fixturing. We knew we needed to streamline and increase our capacity with limited floor space.” And so the search began for CNC machine with a small footprint and a manufacturer with a reputation for fast and accurate production results, which led Tecomet to Schwäbische Werkzeugmaschinen GmbH (SW) in Southern Germany.
Extensive testing delivered the proof
Multi-spindle machining centers from SW had already been discussed at Tecomet back in 2013, as Senior Engineer and CNC machining enthusiast Jason Perry recalls: “Even back then, we thought these machines would be perfect for the type of high-volume manufacturing we perform at Tecomet.” Since the annual forecast of the major volume production cell did not justify the purchase back then, a site visit by SW remained the only result of these considerations. But the idea of multi-spindling left such a lasting impression that it was thoroughly re-evaluated in 2021.
Given the pandemic restrictions at the time, seeing the SW machines in action was out of the question. However, Tecomet was aware of their superior quality and reliability. “This was unknown territory for us. We were the first Tecomet site to explore the possibilities of using SW multi-spindle machining for poly products,” Jason Perry says. “But working with SW to create a user requirement specification based on the existing, validated process gave us the confidence that SW fully understood our needs and expectations.” Extensive development trials and very satisfactory FAT and SAT tests underlined the machines’ performance and compatibility as well as SW’s technical know-how. Together with a comprehensive service portfolio and an extended warranty from 1 to 2 years, it was enough to convince Tecomet to commission the first BA W02-22 machine, despite never having seen it live.
Quick installation, high efficiency
Going forward, everything came together quickly: it only took a few weeks between the first contact and installation. Soon, the first machine was up and running at full production capacity. “This rapid timeline was facilitated by strong and comprehensive support from SW and the high operator-friendliness of the machine,” Peter Grehan emphasizes. “Our employees were able to familiarize themselves with it very quickly.”
Equipped with two spindles with 36,000 rpm and a linear drive technology, the BA W02-22 brings maximum dynamics and efficiency to the multi-step manufacturing process – from the high-quality raw polyethylene material to roughing, semi-finishing, and finishing of the tibial inserts. The plastic tibial inserts replace the cartilage in the knee implant and act as a cushion for the femoral component. “We produce multiple part sizes and thickness for either left or rights knee inserts leading to several different variations,” Jason Perry explains. “Manufacturing these parts involves maintaining tight tolerances and managing material movement post-machining, especially for features with profile tolerances.” To ensure high repeatability and robustness, each process step is fixtured on a different table, which means the fixtures do not need to be switched between operating steps. This allows the machine to run continuously, while each spindle works on a different component at the same time.
OEE consistently higher than average
For Tecomet, manufacturing on the BA W02-22 comes with several advantages: the machine’s horizontal spindle orientation supports the effective chip evacuation, maintaining the quality and consistency of the final product. Additionally, the BA W02-22’s dry machining ability – using compressed air instead of coolant for cooling – results in a cleaner process, which is essential for maintaining surface finish requirements on large articulating surfaces. The machine also requires less space to produce the same volume of parts, having roughly the same footprint as the previous single-spindle machines. And finally, the machine’s easy operability has made it a favorite among the Tecomet employees: “They practically battle over who gets to work on the SW machine,” Peter Grehan says.
Without a doubt, though, the most important benefit lies in the machine’s efficiency, as Peter Grehan emphasizes: “In a nutshell, it’s all about output and OEE. The main advantage of two-spindle manufacturing is having two spindles working on two parts in the same cycle.” The twin rotary table and not having to change fixtures between operating steps significantly reduces operator interaction times. The machine runs nearly continuously. The only down time is for setups between product variants, which is minimum. “This is one of the main reasons for higher OEE we see on the machine from SW,” Jason Perry explains. Peter Grehan adds: “Compared to other machines in the cell, we produce more output per operator on it. The machine has proven to be highly reliable, precise, and efficient. It significantly enhances our production volumes and with the added advantage of 5 axis machining, helps to future proof our machining capability.”
Further expansion on the horizon
Tecomet initially ordered one BA W02-22, but given the positive experience, it was no surprise that the company decided to further expand its production lines and quickly put a second BA W02-22 into operation: “We have grown considerably over the past three years,” Peter Grehan explains. “We plan to further expand this business area going forward and integrate new technologies such as automation and machine tending solutions in order to maintain our position as a leading contract manufacturer for medical devices.” Jason Perry adds: “The collaboration with SW has been very positive and characterized by open communication, transparency, and excellent technical support. And since the machines and their performance have consistently met our production requirements, we are strongly considering adding more SW technology in the future.” But one thing is already clear, getting the SW machines up and running, albeit without ever having seen one operate before, has definitely been a great experience for Tecomet Cork and its COE for plastics manufacturing.
Connection.
Your contact person
for press information:
Angelina Stohp
+ 49 7402 747975
angelina.stohp@sw-machines.com