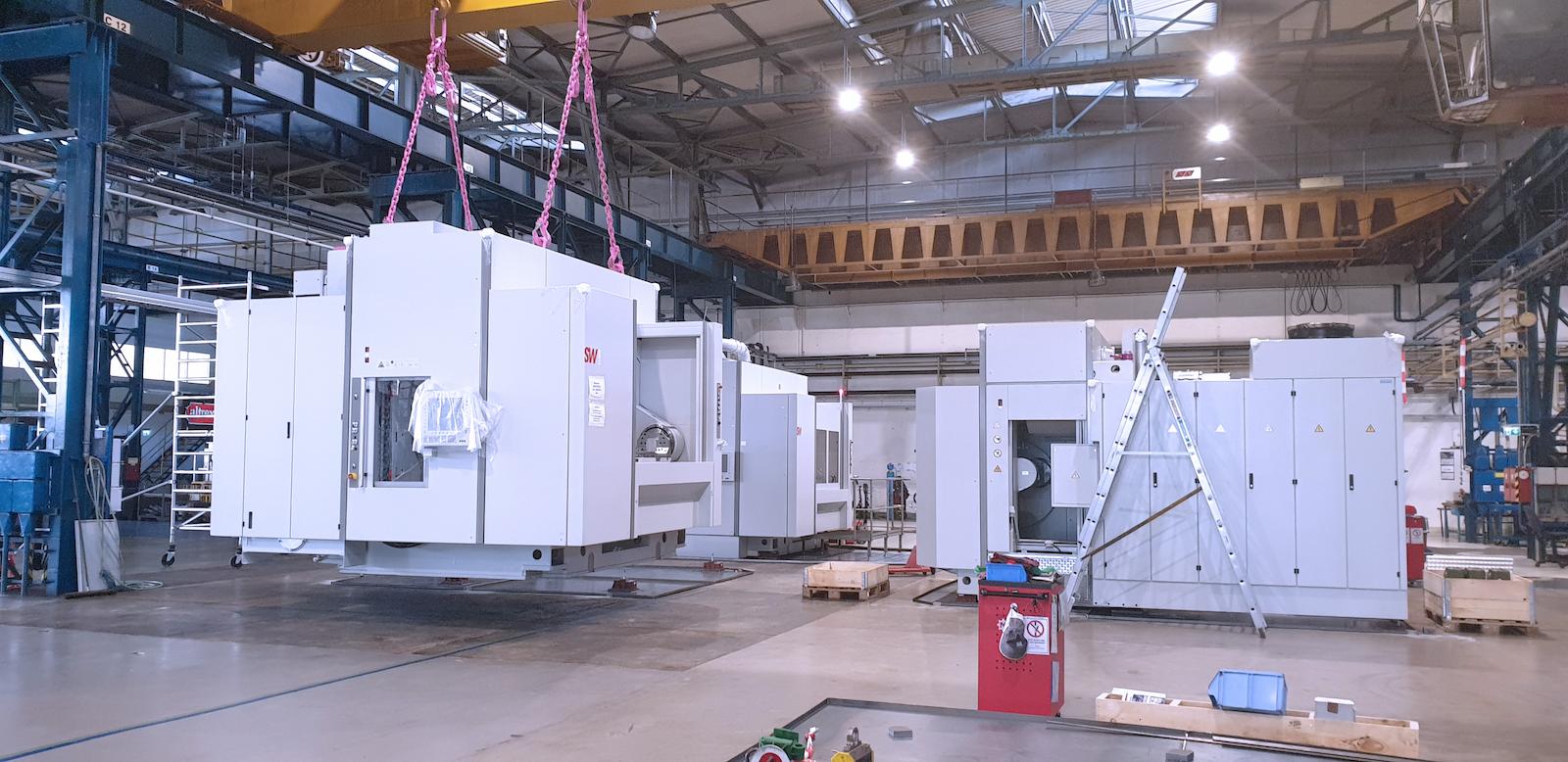
For a new production line for machining cylinder crankcases, HAL Automotive GmbH relies on machines and automation from Schwäbische Werkzeugmaschinen GmbH – and thus realizes the entire project in less than a year.
More than 18.5 million euros in annual sales, 17 SW machines, and just 65 employees: That is HAL Automotive GmbH in Plauen. The medium-sized company processes aluminum castings for the automotive industry. Thousands of vehicle parts such as oil pan tops or cylinder head covers leave the plant in Vogtland every day. Short project lead times and short cycle times are the order of the day. In order to cope with the enormous demands of the automotive industry with such a small workforce, the company relies on full automation and strong partners from the mechanical engineering sector wherever possible. This was also the case in 2019, when a well-known automotive group approached HAL with a major order: It was for the production of more than 600,000 cylinder crankcases per year, which are a central component of every combustion engine. “High precision at high volumes and maximum speed,“ is how HAL Managing Director Bodo Bäsler sums up the requirements for production of the workpiece. However, maximum speed was not only required for machining the parts themselves, but also for setting up the new line. The entire project had to be implemented within a year. By then, the suitable CNC machining centers had to be selected, delivered, tested and commissioned, and the associated automation had to be fully developed and installed – a tight time-frame for a project of this size.
“It was clear to us from the very beginning that the equipment and the automation should come from a single source,“ emphasizes Bäsler. “This is important to us because, on the one hand, it guarantees that everything is coordinated and, on the other hand, it ensures greater efficiency in the project process. Especially in such a tightly scheduled project, this is essential.“
Multi-spindle capability ensures required cycle time
The search was therefore on for a machine builder who could provide and fully automate machining centers with the necessary number of cycles and precision within a few months. “We thought directly of Schwäbische Werkzeugmaschinen GmbH,“ says Bäsler. “We have a very good and long-standing business relationship with SW.“ Three SW systems for the fully automated machining of oil pan upper parts have already been in the Plauen HAL hall since 2014. In terms of performance and durability, the machines are unbeatable, says Bäsler: “We are highly satisfied with the systems. They still have the same spindles in them as when they were delivered in 2014, and that‘s after more than 20,000 hours of operation each.“
For the new crankcase production line, the choice quickly fell on five BA W06-22 machines and five BA W08-22. “As twin-spindle machines with linear motors, these systems achieve the precision and speed required for machining cylinder crankcases while taking up little space,“ explains Bäsler. “In addition, we would have had to choose huge special machines from other machine suppliers for the second machining step, whereas at SW the BA W08 met our requirements. That saved us space and money at the acquisition stage and simplified maintenance later on.“
Complex automation solutions for complex product
Once the machines had been selected, things had to move quickly. Regional sales manager Erik Pfeiffer recalls, “The order was received in December 2019. After that, every day counted for us.“ After just three months, the first pair of BA W06-22 and BA W08-22 machines was delivered to Plauen, followed by the other pairs of machines every week. Parallel to the production of the remaining eight machines, SW was also responsible for the complete automation – from the conveyor technology to the development of the gripper technology and the software.
A particular challenge in the development of the automation was the high variance of parts, as the line had to be able to process a total of six different variants of 3-and 4-cylinder crankcases. The robot had to be ableto grip each of these different parts without damagingthem. At the same time, correct recognition of thepart variant was essential to avoid incorrect machiningsteps. To meet the challenge, SW relied on scanningdata matrix codes and also developed its own gripper for HAL. “For such elaborate automation, the timeline was very tight. We had several programmers working throughout to finish on time,“ Pfeiffer explains. “It paid off that we were frequently on site in Plauen: This allowed us to test the automation sequences live and optimize the production process even further.“
Production line never stands still
After just six months, all ten machining centers had reached their destination in Plauen. The new production line was divided into cells: One BA W06 and one BA W08 each form such a cell together with a robot that sits elevated in front of the machines. “We work with cells and redundancies in all our production lines,“ explains Bäsler. “If one cell fails due to problems or maintenance, the other cells can continue to work. In this way, we ensure that the entire production line never comes to a standstill.“
For the machining of the cylinder crankcases, a total of five such cells are located one behind the other in the line, connected by two conveyor belts – one for blanks and one for finished parts. The blanks delivered by the customer are placed on the blank conveyor, where the data matrix code is automatically scanned and the part variant is determined. To simplify shipping, only blanks of the variant currently being processed are fed into the line; production always remains single-variety. Blanks of the correct variant then continue on the conveyor belt to the machines. An algorithm automatically calculates when the next machining center becomes free and sends the blank to the corresponding cell. An additional supply is automatically replenished in between and ensures that the production line can continue to run fully automatically even when employees take breaks.
Two parts produced per minute
When a blank arrives at the selected cell, the robot picks it up from the conveyor and passes it to the four-axis BA W06-22 for the first machining step, which first pre-machines the sides of the workpiece. The robot then transfers the workpiece for further machining to the BA W08-22, where the workpiece stands on end in the machine and is machined on five axes.
In both machining steps, two spindles halve the cycle time; a double swivel carrier permits loading and unloading of the systems during machining. Both machining steps together take a total of 9.4 minutes. With five cells and two spindles per machine, two parts are thus completed every 57 seconds. The finished workpieces are placed on the corresponding conveyor belt, which takes them directly to the peripherals including the washing machine at the end of the production line. The finished product can then be packaged and shipped. Since its commissioning in summer 2020, the entire production line has been running around the clock in three shifts. Thanks to full automation, just three to four employees are needed in each shift, otherwise ten to fifteen would have been required. One employee places the raw parts on the belt, two carry out visual inspections during the process, and the last is responsible for packaging.
Cooperation at eye level
Looking back on the entire project and the collaboration with SW, Bäsler sums up: “Overall, we are really very satisfied. Together with SW, we even implemented the project faster than expected: Even before the dead-line, we were able to present the first production-ready parts to our automotive customer. The machines and automation are also doing an excellent job and fully meet our requirements.“
The most important success factor from his point of view is the long-standing partnership with SW. “For many years now, we have held SW in high esteem as a business partner for precisely this reason. If there are difficulties, we can rely on an expert being there quickly, looking at the problem on site and pragmatically seeking solutions with us.“ Pfeiffer confirms the good cooperation: “As a former mechanical engineering company, HAL brings enormous competence in the field of electronics and mechanical engineering. We really work together at eye level.“
The next joint project is already implemented
Considering the successful project for the cylinder crankcases, it’s no wonder that HAL also turned directly to SW for its next order: The company is once again relying on SW solutions for the production of cylinder head covers. Four more BA W06-22 were delivered to HAL in early 2023; the first finished parts went to the customer‘s engine plants back in the spring. “Even more than with other automotive parts, cylinder head covers are all about precision: here, every μ really matters in the machining process,“ says Bäsler. “That‘s where it‘s a good feeling that we can rely on SW‘s reliability, both in terms of equipment and cooperation.“
Connection.
Your contact person
for press information:
Angelina Stohp
+ 49 7402 747975
angelina.stohp@sw-machines.com