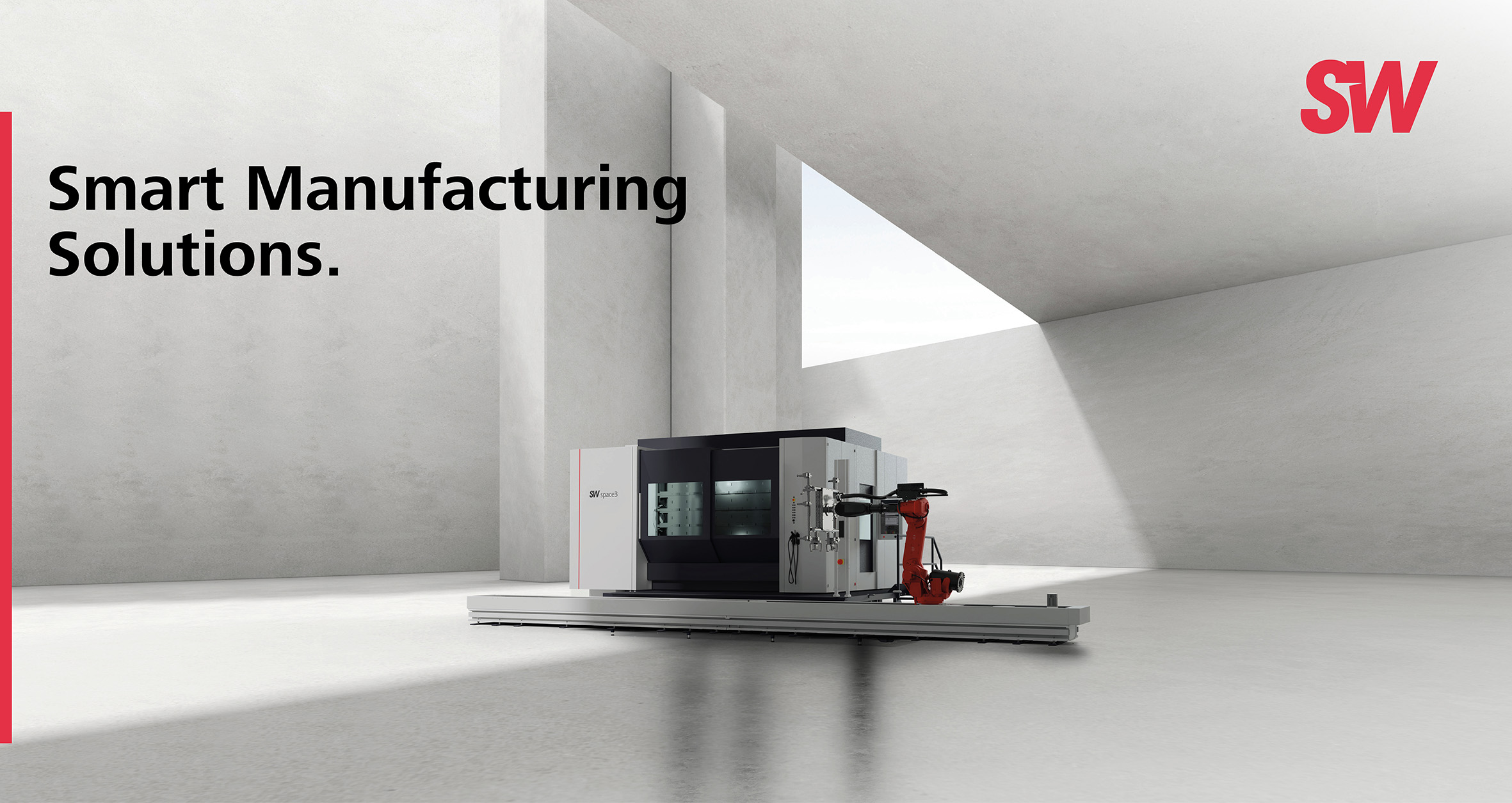
It has revolutionized automotive production: In giga casting, large structural automotive components are produced in one piece, using high pressure die casting. The process is a challenge – not only for die casters. The following article sheds light on why the machining of giga components is a difficult undertaking and what solutions can look like.
Following Tesla’s success, companies like Volvo are following suit: In giga or mega casting, structural components such as the underbody of a car are no longer welded, glued, or screwed together from many individual parts, but cast in one piece. The process drastically reduces the number of components produced and eliminates most joining operations. This results in savings throughout the production chain. In addition, giga components reduce the weight of a vehicle, which is particularly advantageous in the field of electromobility: less weight means greater energy efficiency and therefore a longer range for the vehicles.
However, these advantages are accompanied by complex requirements in production. Many of them come from the die casting itself, from the huge casting molds and their temperature control to subsequent cooling and the associated component distortion. Even after the die casting has been successfully completed, giga components remain challenging, as Product Manager Michael Kreuzberger from SW points out: “Discussions about giga casting have mainly focused on the die casting process itself up to now. However, the complexities of giga components go further. Machining these large castings also presents several challenges that need to be considered.”
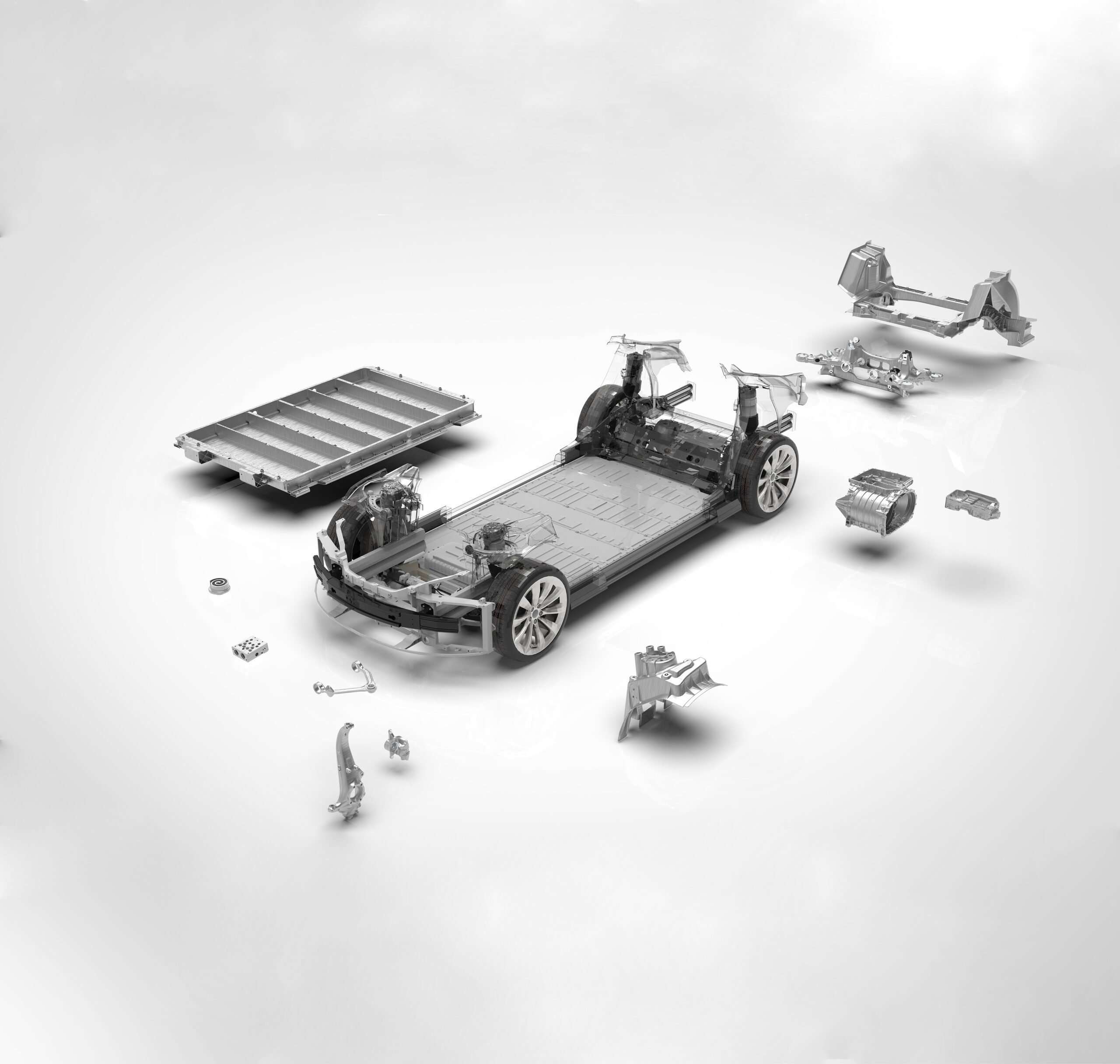
Large machines, high space requirements
Some companies have already developed special large machines for die casting, such as Tesla’s Giga Press. Reality is much different when it comes to CNC finishing. It is often still done on portal milling machines from the large-parts manufacturing industry. “The components from giga castings are simply much too large for conventional CNC machining centers. The parts don’t fit in the machines,” Kreuzberger explains. “On the other hand, the systems from large-parts manufacturing are actually too large and, above all, too sluggish. Efficient machining is hardly possible on these single-spindle portal milling machines. Machining times are too long and loading and unloading is too time-consuming.”
So, on the one hand, companies face enormous space problems. After all, the die casting machines required for giga casting alone can reach the size of a house. Add huge portal milling machines to that, and many production halls quickly reach their limits. And only few companies have the same option as Tesla, namely building a new, greenfield production hall of the necessary size.
Cycle times do not meet automotive requirements
Even if sufficient space is available for large portal milling machines, their long machining times are problematic in the fast-cycle automotive industry. One reason for this is the use of ball screws to translate rotary motions. Kreuzberger explains: “In aluminum machining, the non-productive times are significantly higher than the pure machining times. The larger the workpieces are, the longer the distances the feed axes have to cover, for example during a tool change. Since ball screws have lower accelerations and speeds, the non-productive times get even longer.” In short, machines from the large-part production sector generally cannot deliver the cycle rates required in the demanding automotive industry. Herein lies a major challenge in machining giga parts: achieving typical speeds for the automotive industry on workpieces this large.
Another challenge lies in the sensitivity of the components. Since die casting creates stresses in the workpiece, large-volume castings are susceptible to warpage. In electric cars in particular, the wall thicknesses of the components have to be as thin as possible in order to save weight. This adds to the warping risk. “The precision of the machine is not the problem. Both large portal milling machines and smaller machining centers can easily achieve the required accuracies,” clarifies Kreuzberger. “Rather, it is a question of optimally matching the workpiece to the clamping device in the machining center and the gripper technology to avoid distortion during machining.”
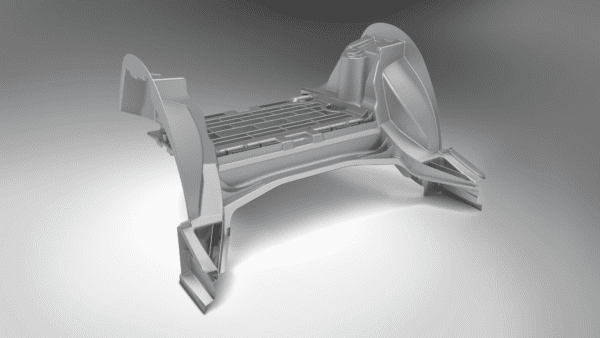
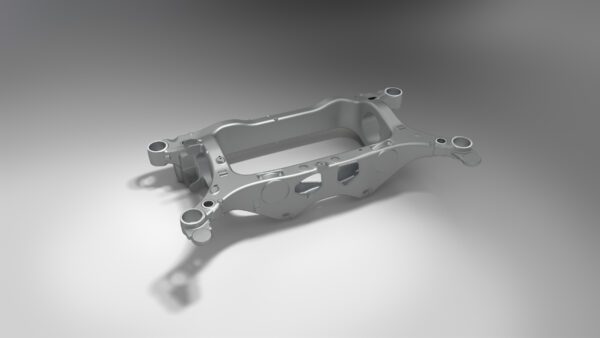
Higher speed thanks to linear motor
A solution for the sensitivity of giga components during machining: “The clamping device must be developed specifically for the respective component to fit exactly. Close cooperation with the machine manufacturer is crucial for the best individualized result,” says Kreuzberger. “At SW, we have our own department that is exclusively concerned with ensuring optimum coordination between the clamping device and the workpiece in close consultation with our customers.”
Things get more complex when it comes to the challenge of required cycle rates. Here, suitable machines with high dynamics and the necessary space for the giga components are required. In any case, users should opt for systems with linear motors. The direct drive of a linear motor generates the desired movements without mechanical transmission elements. As a result, it achieves maximum accelerations and the highest traversing speeds, while also operating wear-free. “The fastest CNC machines on the market all use linear and torque motors, including most of our own machines,” says Kreuzberger. “We also rely on a weight-optimized design. This allows us to minimize non-productive and cycle times. Our machining centers achieve acceleration values of over 2g and rapid traverse speeds of 120 m/min.” To harness this speed for larger workpieces, SW launched the BA space3 in 2021. The machine combines high cycle speeds with the space needed for large castings. Only multi-spindle machines are faster.
New SW machine focuses on multi-spindle capability
Currently, there are hardly any multi-spindle machines for large castings on the market. But SW is already working on a machine that will introduce two spindles into its ‘space’ series. “In contrast to our other multi-spindle machines, the two spindles will operate completely independently of each other,” says Kreuzberger. “We are using two autonomous three-axis units to allow maximum flexibility with different components.” For medium-size components, both spindles can each work on one component in parallel as usual. For larger components where only one workpiece fits in the machine, both spindles can work simultaneously on the same piece and change tools independently of each other. A double swivel carrier allows for parallel loading and machining and ensures a further reduction in cycle time. As a result, giga parts such as the rear underbody of a Tesla can be machined in just 1.5 minutes – almost twice as fast as with single-spindle machines.
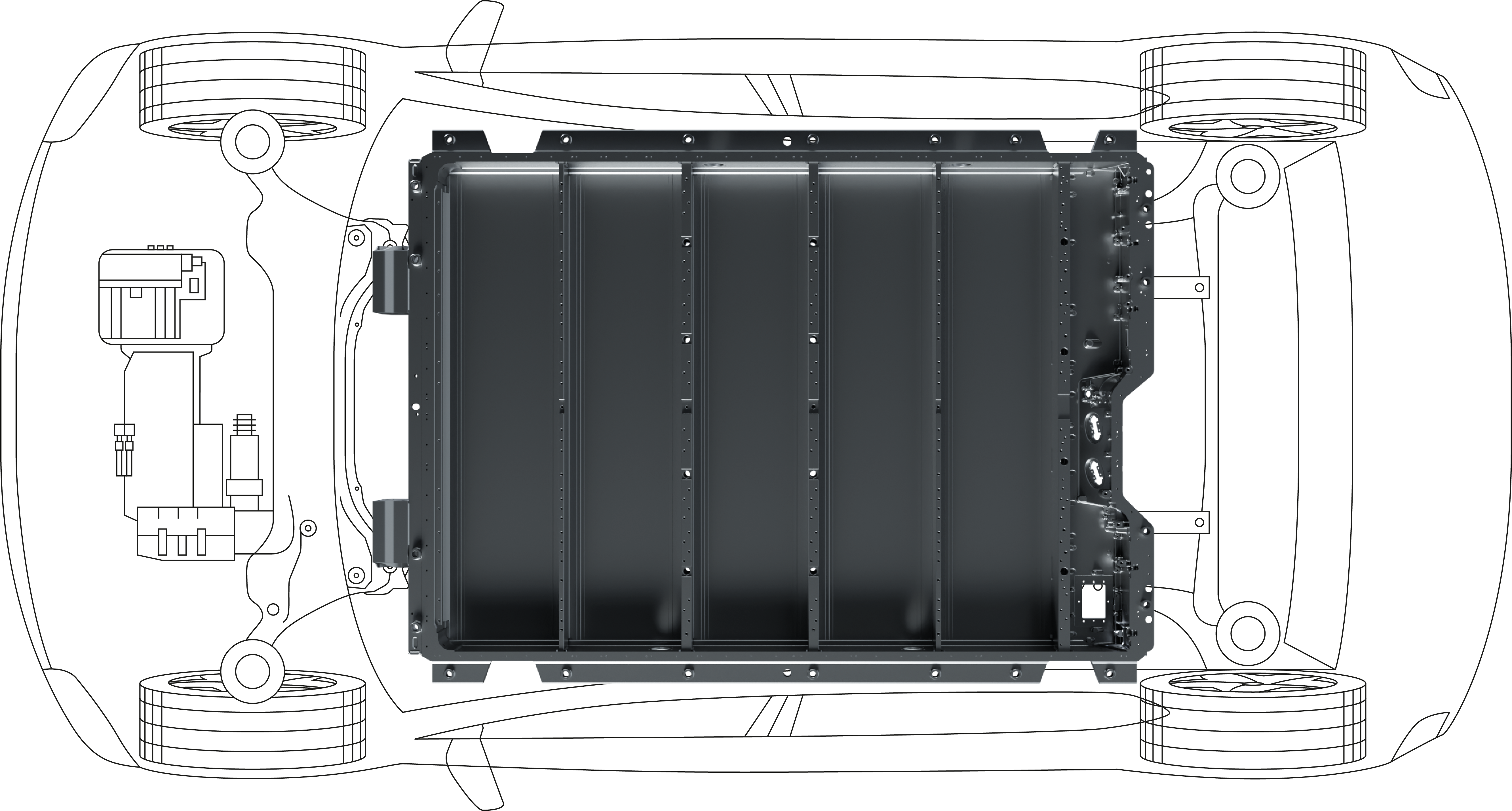
“With the rapid development of electromobility, giga-casting will continue to gain in importance over the next few years,” concludes Kreuzberger. “Other automotive manufacturers are also currently examining the advantages and disadvantages of using large castings. Asian original equipment manufacturers (OEMs) in particular are already relying heavily on giga castings and are successfully installing them. We want to do our part to ensure that the advantages of this process outweigh the disadvantages and that the machining challenges can be easily overcome as well.”
Connection.
Your contact person
for press information:
Angelina Stohp
+ 49 7402 747975
angelina.stohp@sw-machines.com