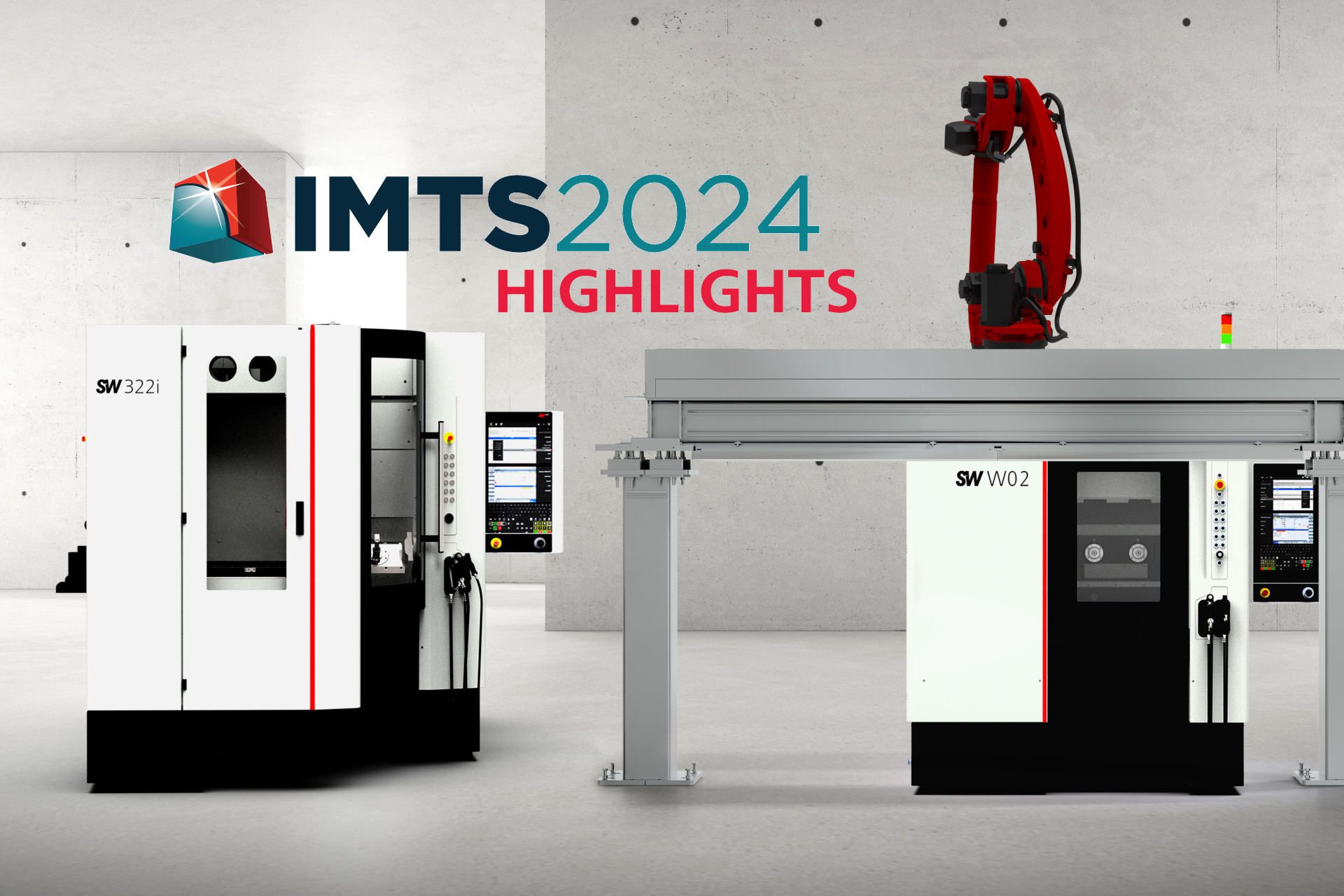
September 9th – 14th 2024
Thanks to our Demonstration Partners
CNC Machine and Automation Solutions at IMTS 2024
SW North America featured live machine and automation demonstrations for the entirety of IMTS 2024 at booth #338250!
The demonstrations included live machining across industry verticals, including EV, automotive, medical, aerospace, heavy trucking, agriculture, and construction, on the BA 322i and BA W02-22. Additionally, SW hosted live manufacturing automation demonstrations of a battery housing for an EV in the automotive space.
Our goal is to ensure maximum productivity and flexibility in our machines, automation, and systems to help manufacturers like you shorten cycle times, free up floor space, gain higher production capacity, lower energy consumption, and reduce labor needs.
SW North America at IMTS 2024
Machines and Automation Highlights
BA 322i
BA 322i
The BA 322i is designed to function as an independent manufacturing cell that can store enough workpieces for an entire shift.
This twin-spindle horizontal machining center doubles output while using less floorspace and less energy.
The integrated 6-axis robot utilizes the vertical workpiece storage tower to load and unload workpieces in parallel to machining time thanks to the double swivel carrier. The monoblock and box-in-box design are proven SW standards, providing more stability and precision.
This plug & play solution is perfect for the machining of impellers, brake calipers, scroll compressors, ABS valve bodies, and more.
The BA 322i is designed to function as an independent manufacturing cell that can store enough workpieces for an entire shift.
This twin-spindle horizontal machining center doubles output while using less floorspace and less energy.
The integrated 6-axis robot utilizes the vertical workpiece storage tower to load and unload workpieces in parallel to machining time thanks to the double swivel carrier. The monoblock and box-in-box design are proven SW standards, providing more stability and precision.
This plug & play solution is perfect for the machining of impellers, brake calipers, scroll compressors, ABS valve bodies, gun slides, and more.
BA W02-22
Experience shorter cycle times and higher productivity with direct drives. Linear motors and torque motors generate the desired movements directly, without mechanical transmission elements and therefore operate wear-free and without mechanical backlash. The acceleration of linear motors is particularly important. In SW machining centers, they achieve acceleration values of up to 2g and rapid traverse speeds of 120 m/min. And this is with maximum precision.
GANTRY SOLUTION: TopRob7
With the modularly expandable gantry solution and the 7-axis robots “TopRob7”, we optimally link your CNC machining centers and peripheral stations to form highly productive production lines. We arrange the TopRob7 on a gantry axis at a height of around 2 meters. Several robots can work independently of each other on one gantry axis. TopRob7 loads and unloads the machines and systems process-oriented from above. You do not need protective fences, so you can save valuable space in production. Above all, your operators have a clear view of the work areas, and all machine tool components are freely accessible during maintenance work.
BA space3
The BA space 3 features a working range of 3,000 x 1,800 x 875 mm on the X-, Y- and Z-axes respectively for precise and efficient production of battery housings, subframes and other large structural components in the automotive, EV and aerospace industries. On each of these axes, the HSK 63 spindle can reach a rapid traverse of 120 m/min, with a chip-to-chip time of 4-4.25s.
AUTOMATION MODULE: FloorRob
With the FloorRob6 and FloorRob7 Automation Modules, you can quickly and easily load and unload machines from the front. Depending on the version, the time saved during the robot’s movement when loading can be as high as 45% compared to manual loading procedures. Another advantage is the ability to load multiple machines automatically. And, in contrast to the static FloorRob6, the FloorRob7 can also move back and forth along the entire traversing axis. This allows the linking of machines.